Why is the Iveco engine popular? FPT Technology Day Shows Global R&D Strength
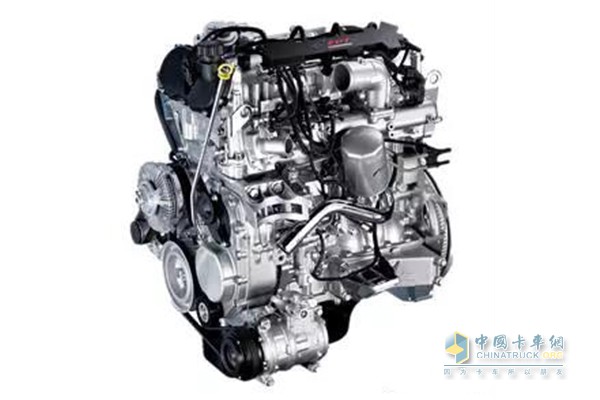
On October 30, 2017, we held the Fiat Power Technology 2017 Technology Day at the CNH Industrial Village in Turin. Media from the Asia Pacific region visited the FPT Turin Test Center to learn about the technical strength of the factory research center as a global benchmark.
Where is FPT strong? FPT Technology Day unveils its mystery!
For many years, FPT has been working on engine technology solutions during its long development. In 1938, FPT developed and produced turbocharged heavy-duty engines in the world. In 1985, it developed direct-injection light diesel engines. In 1989, it developed an exhaust gas recirculation diesel engine for light commercial vehicles. In 1998, it produced variable applications. Heavy-duty diesel engines with cross-section turbochargers were developed in 1999 and 2002 for commercial and non-road electronically controlled common-rail systems.
Turbo heavy duty engine
FPT has seven R&D centers in the world and more than 140 test equipments. Each R&D center has its own expertise. For example, in Albon, Switzerland, as a development center for cutting-edge technologies, a common-rail system was developed in 1999 and Hi-eSCR technology was developed in 2012.
Iveco Research Offices
In Europe, FPT has 4 R&D centers. In addition to Albon, France Fécam is responsible for the custom development and verification of generator sets; Italy has two R&D centers and Torino has the largest number of test benches currently, focusing on gas technology development (Fiat Power Technologies has 51 engine test benches, 30 drive train test benches, 8 climate experiments and special equipment rooms, and 1 chassis-to-hub gantry in the world; Foggia, Italy, is responsible for the development of global natural gas technology as Turin. .
The R&D center in Burr Ridge, United States, is dedicated to engines used in Case New Holland and other external customers in North America. Betim, Brazil, is an engine R&D center serving the Latin American market. In Chongqing, China, SAIC Fiat Hongyan (joint venture), which is well-known, is committed to supporting the customized requirements and application implementation of the Asian market.
The FPT Turin Test Center serves as a model for “green factories†to increase energy efficiency and reduce CO2 emissions. "Innovation" is the driving force for sustainable development. The Turin Test Center is a global benchmark for the development and validation of engines and aftertreatment systems. It also develops axles and transmission systems for its New Zealand subsidiary brands.
Since 2014, FPT has been committed to zero pollution in the environment, continuous improvement in continuous exploration and development, and the spirit of innovation has spread to the entire R&D center, including all 8,000 square meters (more than 30,000 square feet) and 400 employees. Participation includes engineers, professional mechanics and other professionals. In recent years, the Torino Test Center has introduced new testing capabilities designed specifically for real-world road simulation tests.
Today, the entire test center already has up to 90 test benches. For example, our groundbreaking climate simulation test rigs can simulate -35 to 40°C temperature and simulate up to 4,000 meters above sea level.
There are other test benches for testing light hybrid vehicles that can be used to simulate power battery power supplies. In addition, we also have the ability to simulate a maximum tilt of 45 degrees in the vehicle, these capabilities can help us to simulate some special conditions, including agricultural machinery, ship, mining equipment.
Advocating sustainable development and reducing energy consumption also apply to the FPT work environment, such as the maintenance and updating of office buildings. In Trin, Germany, we replaced the traditional lighting system with LED lighting. At the same time, we introduced a solar-powered facility to provide electric power and hot water for the entire plant. This is our philosophy of constantly advocating change and continuous improvement.
Based on the FPT's “Green Heart†all action plan, 2016 has produced more than 2.7 million kWh of energy.
Raschel lace machines indicate a big machines range, which includes Multibar Raschel Machines, Raschel Jacqaurd Machines, Fall-plate Raschel Machines, Multibar Jacqaurd Raschel Machines and others. Multibar Raschel machines indicate that pattern bars amount above 18, while Raschel Jacquard Machines usually refer to curtain machine, such as TH-4/1F type and its upgraded machine types Besides, high speed elastic textile machines RSJ4/1 and RSJ5/1 are also belong to Raschel Jacquard Machine.
As market-tested machines, A-ZEN Brand Raschel Lace Machines enjoy good reputation from market because of its stable quality and 360°services.
A-ZEN Raschel Lace Machines adopt advanced technology, for example electrical shogging system, flexible pattern needles, user-friendly computerized operation system, as well as good quality spare parts.
A-ZEN Academy provides a detailed training course for new users, the course covers fabric analysis, designs development, machine operation and maintenance, etc.
Technical Data:
Working Width/Gauge: 134", 200", 242"/ E18,E24;
Working Speed: 50-750rpm (Depends on yarn and designs, Fall-plate machines 550rpm);
Pattern Drive System: EL Drive;
Yarn Let-off Device: Electronical Yarn Let-off System;
Fabric Take-up: Electronical Fabric Take-up System;
Batching Device: Electronical Batching Device;
Laser Stops Detector;
Online Service Supported.
Details please check machine leaflet.
Raschel Lace Machines,Multibar Raschel LACE Machines,Raschel Jacquard Machines,Fall-Plate Raschel Machines,Warp Knitting Machine
CHANGZHOU A-ZEN TEXTILE TECHNOLOGY CO.,LTD , https://www.tricotmachinery.com