Digital Oilfield Station Control System in the Background of Internet of Things
2. Digital Oilfield Station Control System Project Oil and gas field production is a multi-disciplinary and interdisciplinary industry. The operation modes mainly include exploration and development, development and production, oil and gas processing, oil and gas transportation, and oil and gas sales. With the constant exploration of new resources, the rolling development model has gradually taken shape. In the course of production and operation, massive amounts of raw data have been produced, and informationization has become an indispensable part of the production of oil and gas fields. The rapid development of today's information technology has accelerated the advancement of oilfield information technology. In order to ensure the timeliness and accuracy of the production of real-time data, the front-end process requirements must be clearly defined. The main objects of remote monitoring and analysis of oil and gas field production are production sites such as oil wells, gas wells, water injection wells, metering systems, and crude oil processing stations.
1) The main parameters of the pumping well are load, pressure, temperature, three-phase current, three-phase voltage, power, torque, and other data, and form a professional graphical data to realize the real-time diagnosis of the well production conditions;
2) The data collected by gas wells are the wellhead pressure, temperature, and flow rate, such as the temperature and pressure after the primary valve, the temperature and pressure after the secondary valve, and the temperature and pressure after the tertiary valve. According to different process requirements, it is also possible to collect the pressure of the casing and remove the flow of water;
3) Water injection well production remote monitoring system is mainly concerned with the parameters of pressure, flow, etc., according to the pre-set the amount of injection, compared with the injected amount, with reference to the current real-time pressure, automatically adjust the valve opening;
4) The measurement system is an important reference for the production of oil and gas fields, mainly based on crude oil measurement. Although there are differences in the metering process, the main goal is to calculate the reference output. The main monitored variables are manifold pressure, manifold temperature, valve status, and metering fluid level. Each fluid volume is calculated by the coefficient and uploaded to the central control system.
5) The crude oil processing station is the terminal process in the entire crude oil production and is responsible for the separation and measurement of oil from various front-end oil production points (such as oil wells), metering stations, and oil transfer stations, and crude oil, water, and natural gas for mixed crude oil. Separation, realizing crude oil purification, sewage treatment, wastewater reinjection, natural gas processing, crude oil export and other technological processes, is the final process to achieve finished crude oil, the quality of external transport of crude oil, natural gas is essential. Due to the relatively complicated process involved, equipment process equipment, and high safety requirements, the control of the entire station's process and equipment is realized through the setup of control stations, process IO, remote IO, engineer station, and operation station equipment to achieve separation measurement processes and crude oil treatment processes. , Sewage treatment process and reinjection process.
Digital oil fields will lead to large-scale terminal acquisition equipment, and the convenience of implementation and maintenance must also be taken into consideration. Automated production of oil and gas fields has achieved reductions in staff efficiency. When large-scale automated systems need to be deployed, their simplicity will be simpler on the current basis. Wireless communication can solve this problem very effectively. Common mode, special products, wireless communication, etc. greatly reduce the difficulty of on-site construction and large-scale construction can be implemented.
The production environment of the oil and gas field is very harsh, and the desert must accept the challenge of extreme temperature. In the coastal areas, the high humidity and high corrosion test are also required. Because of the inconvenience of the power supply, the automation product also needs low energy consumption. Based on the limitations of these conditions, the general market PLC is obviously not competent, that is, more professional RTU products are needed to perform on-site automation control.
2.1 Equipment Requirements General requirements for on-site instrumentation:
â—Integrated design, wireless data transmission â—Micro power consumption design, precise power management â—One-time lithium battery, solar power supply, one-time lithium battery with solar energy in time â—In line with industry standards, with channel spread spectrum in line with IEEE802.15.4 wireless standard, channel Use direct sequence spread spectrum technology to avoid interference and improve reliability. â— Set the scanning interval as required. â— The protection level is not lower than IP65. The explosion-proof level is not lower than ExdIIBT4. It can be directly applied to explosion-proof applications. â— Operating temperature -40°C~+ 70°C
◠Operating Humidity 5%RH~95%RH
Field Controller General Requirements:
â— Professional products, reasonable structure. With strong adaptability, directly applied to the industrial site â— Flexible communication method, with RS232, RS485, EtherNET and other communication interfaces â— Standard communication protocol, ModbusRTU/ASCII/TCP, TCP/IP
◠Real-time data collection function ◠Active failure reporting function ◠Efficient engineering development tools, in line with IEC61131-3 standard, support LD, FBD, IL, ST, SFC five programming languages ​​◠Friendly human-machine interface ◠Powerful hardware system, 32-bit ARM processor, embedded real-time multitasking operating system (RTOS)
â—Advanced redundancy/fault-tolerance mode â—Operating temperature -40~+70°C, working humidity 5~95%RH, adapting to various harsh environments â—Equipped with CE certification, achieving EMC electromagnetic compatibility level 3 â—The whole protection class IP65
2.2 System Structure The central control room is the core of the digital field automation production system. It collects and monitors all front-end system data.
The monitoring system SCADA system can be roughly divided into 3 levels. The first layer is the data acquisition layer, consisting of an RTU and a meter to complete the collection and preprocessing of on-site raw data. According to design requirements, it can also realize on-site data storage to ensure the continuity of data after communication interruption; layer 2 is the data monitoring layer. In this layer, a variety of software will be used to remotely simulate the site, real-time data monitoring, real-time alarm. This layer can be divided into a sub-control center and a master control center according to the corresponding management mode, and a large amount of historical data can also be stored according to design requirements. The third layer is a data application layer. Analyze and collate the collected data at the application layer and implement multiple forms of distribution as needed. Many companies in the industry have extremely stable products and rich system integration experience in the data acquisition layer, data monitoring layer, and data application layer.
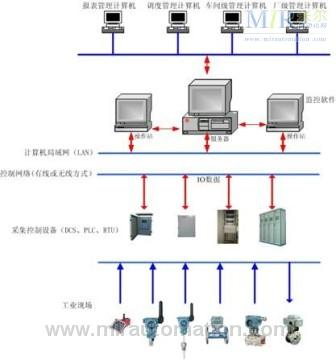
Figure 1: System Architecture
The system composition station control system generally uses RTU/PLC system, the system includes the following parts:
1. Server: Including I/O server, monitoring and alarm server, report server, historical trend server, etc. The server can double as an engineer station or operator station.
2. Control station: including main control unit, I/O module, power supply module and standard cabinet, I/O module completes on-site signal acquisition, engineering unit conversion, continuous and discrete control, main control unit passes 100Mbps high-speed Ethernet and operation station Servers such as servers and advanced computers constitute an enterprise-class intranet network.
3, the communication system: including the system network and control network, fully support the C / S structure. The system network is responsible for the communication between the field control station and the operator station; the control network is responsible for the communication between the control station and the I/O modules, using the fieldbus protocol.
4, a meter: including the general 4 ~ 20mA meters, valves, flow meters, etc., through multi-core armored cable and I / O modules connected.
The structure station control system is divided into two layers of networks. The first floor is a fieldbus network that connects the I/O, substations, and host controllers. The other is the control network, which is used to connect the field control station with the operator workstation.
The core of software software is the monitoring configuration software, which completes functions such as data acquisition, data processing, monitoring, and alarm management. DMS database management software provides secure and detailed database management of the entire station control system data. The SQL/ODBC module in the software enables the real-time data of the configuration software to be easily connected to the database.
3, station control system selection According to the requirements of digital oilfield station control system, you can choose cost-effective RTU / PLC products, especially national brand products, compared with foreign brands in recent years, in the accumulation of experience in domestic enterprises do not account for Advantages, we do not have much difference in terms of technology alone. From the perspective of R&D, foreign brands have already built R&D centers in China, and R&D and manufacturing are localized. There is no difference between a purely foreign system and a Chinese system. It is just a matter of brand differences.
Domestic controller manufacturers such as Hollysys, Zhejiang University, Beijing Security, etc., have each launched their own station control system products. Among them, Beijing Safety Control has been engaged in the production, R&D and system integration of automation (digital) products in oil and gas fields. Beijing Ancon's SuperE50 series RTU is a new type of station-controlled RTU product that has been developed for years of station control system development and engineering experience, enabling the collection of industrial field signals and the control of equipment. The product uses advanced 32-bit ARM technology and an efficient embedded operating system. The entire system is powerful, easy to operate, and highly integrated. Not only competent in logic, timing, counting control, but also complete data processing, high-speed counting, analog control, PID, RTD, TC, communication networking and other functions. Its program development is convenient, accords with IEC61131-3 standard, supports LD, FBD, IL, ST, SFC five kinds of programming languages, can form the control system with upper computer, realize distributed control.
4. To achieve the goal of a digital oilfield station control system based on the Internet of Things technology, establish a set of IoT systems that cover the entire process of oil and gas production and processing, to achieve automatic production data collection, interlocking control of key processes, visual display of process flow, and production process The integrated information platform for real-time monitoring achieves the goal of strengthening safety management, highlighting process monitoring, and optimizing management models to achieve optimal organizational structure and increase efficiency. The concrete realization goals are as follows: (1) Intelligent management of oil and gas production and processing systems â— Realization Data collection and real-time monitoring of oil and gas wells and station depots.
â— Automatic emergency treatment when the oil and gas processing system fails.
(2) Safety and environmental protection at the construction site to achieve humane management â— Alarms for production anomalies and failures, fault patrols, and reduction of the workload of front line employees.
â— Ensure the safety of field operators.
(3) Scientifically guide production and reduce the cost of oil field development â— Optimize the organizational structure, control the total number of employees in the front line, and increase production without increasing people.
â— Through the real-time analysis of production data, the number of well stoppages such as oil well wax cards can be reduced, and the production rate of oil wells can be increased.
â— By monitoring the temperature of crude oil gathering and transportation, normal temperature transportation of low-temperature production in winter can be realized and energy consumption can be saved.
Our company was set up in 2002.We are using the advanced cold punch technology to produce spark plug which is similar to NGK and Champion technology.With such technology, the metal shell and ceramic are better protected the quality of the spark plug are more stable to get avoid from air leaking and broken.Our spark plug products are ranged into more than 100 models with an anual out put of 6 million pcs. Besides the advanced technology,we also have a strong advantage of automatical production.Most of our production device is automatical that we have very high,efficiency and stable quality.Throughout such years of developing,we have gained a good reputation at domestic motorcycle manufacturer.Furthermore,our products have been exported to South East Asia, Middle East, Australia and so on. Revolution,refine and devotion are our principal of working.Welcome to visit us and raise your demand and your comments request are our target to strive.
Spark Plug A7Tc,Changing Spark Plugs,Automotive Spark Plugs,Auto Normal Spark Plug
LIXIN INDUSTRIAL & TRADE CO.,Limited , https://www.jmsparkplug.com