The harm of static electricity to chemical production
Chemical companies, especially pharmaceutical and chemical companies, often use and transport flammable and explosive materials during the production process. Since static electricity is generated by processes, devices, or personnel, static electricity may not be controlled if it is not controlled effectively. The accidents caused by static electricity have appeared many times in fine chemical companies. When foreign security experts check the safety of domestic chemical companies, they pay great attention to the inspection of static electricity prevention measures. Therefore, it is necessary to carefully analyze the causes of static electricity in production. , Predicting its hazards, and paying enough attention to static electricity prevention work, and implementing static electricity prevention measures.
First, the harm of static electricity
1. There are three kinds of electrostatic hazards: First, it may cause explosions and fires. Explosions and fires are the biggest hazards of static electricity. Although the energy of static electricity is not great, but because of its high voltage and easy to discharge, there will be static electricity sparks. In an inflammable and explosive place, it may cause a fire or explosion due to electrostatic sparks.
2. It may cause electric shock. Electric shock due to static electricity may occur when the human body approaches a charged object, or it may occur when an electrostatically charged human body approaches a grounded body. Electric shock can cause accidents such as falling and falling. Electric shock can also cause staff tension and affect work.
3, it may affect production. In some production processes, the elimination of static electricity will affect the normal operation of the equipment or reduce the product quality. In addition, static electricity can cause malfunctions of electronic automatic components and cause secondary accidents.
Second, there are four main forms of static electricity in chemical companies
1. It is the accumulation of static electricity due to material flow. The use of toluene, isopropyl ether, ethyl acetate, methanol, alcohol and other inflammable and explosive organic solvents used by chemical companies are discharged into storage tanks in tank trucks → loading tanks into transit tanks → transfer tanks into reactors → reactors In the centrifuge or layered transfer barrel process, if you use a plastic tube with no electrostatic discharge function or a metal tube with poor static conductivity, and the material flow rate is greater than 4.5 meters per second, static electricity will be generated. As the material flow time increases, static electricity accumulates.
2. The material generates static electricity during rotation. If the electrical conductivity of the equipment is not good, the materials in the reactors and centrifuges of the workshops can accumulate static electricity during the long-term high-speed rotation.
3. In the process of rapid transportation of materials, if the transportation equipment is not reliably grounded, electrostatic accumulation may easily occur due to violent shaking.
4. The chemical fiber and wool clothing worn on the body can easily generate static electricity by friction during wear, removal or limb shaking. Chemical fibers, woolen towels or cloth pieces can also generate static electricity during the wiping of equipment, valves and pipes.
Deep Drawing is a Sheet Metal Fabrication process in which a sheet metal blank is radially drawn into a forming die by the mechanical action of a punch. It is thus a shape transformation process with material retention. The process is considered "deep" drawing when the depth of the drawn part exceeds its diameter. This is achieved by redrawing the part through a series of dies. The flange region (sheet metal in the die shoulder area) experiences a radial drawing stress and a tangential compressive stress due to the material retention property. These compressive stressesesult in flange wrinkles (wrinkles of the first order). Wrinkles can be prevented by using a blank holder, the function of which is to facilitate controlled material flow into the die radius.
Deep drawing is one of the most widely used processes in sheet metal forming. It is used in a wide range of production processes. For example, it is used by the automotive industry to manufacture car parts; it is also used for making household items such as stainless steel kitchen sinks. 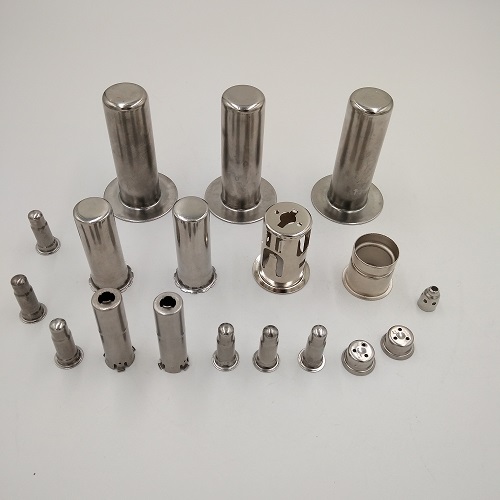
Deep Drawing
Deep Drawing,Aluminium Deep Drawing,Deep Drawing Machine,Deep Drawing Tool
Nanpi Jian Tong Hardware Manufacturing Co., Ltd. , https://www.sheetmetals.nl