Research and Discussion on Combustion Control of CFB Boiler
Introduction CFB boiler combustion technology has a low nitrogen oxide emission, can achieve direct desulfurization in the combustion process, a wide range of fuel adaptability, high combustion efficiency and a large range of load adjustment and other advantages, has become the current choice for coal clean combustion energy saving and environmental protection.
CFB boilers also have shortcomings in the operation process, especially in the initial stage of operation, such as serious abrasion of the heating surface, prominent slagging problems, serious ash leakage in the plenum, and long start-up boiler time. However, as long as the understanding of the characteristics of the circulating fluidized bed technology, to ensure that the boiler design is reasonable, strengthen the equipment management, strengthen the inspection and treatment of the weak links in the boiler, the boiler operation will gradually reach a better level. Based on the investigation of CFB boilers in recent years, we briefly describe the following issues that need to be noted in the boiler combustion control.
1. Temperature control Temperature measurement is one of the key parameters for the safe and stable operation of a circulating fluidized bed boiler, which mainly includes the measurement of the temperature of the material layer and the return temperature.
The temperature of the material layer refers to the temperature of the fluidized material in the combustion dense phase region, which mainly determines the reaction speed, solid product distribution, and pore plugging characteristics of the limestone, thereby affecting the desulfurization efficiency and the utilization rate of the limestone. When the combustion temperature is less than 800°C, the calcining rate of limestone is slowed down, which reduces the surface area available for reaction. As a result, the desulfurization reaction rate decreases, and the effect of limestone capturing SO2 in the bed material deteriorates, making it difficult to achieve effective desulfurization; Below 750T, the desulfurization reaction hardly proceeds anymore, resulting in low-temperature coking and extinguishing. On the other hand, when the combustion temperature is too high (>920°C), the desulfurization efficiency decreases despite the high reaction rate. The reason is that the temperature is too high, it will cause premature blocking of the surface pores of limestone particles, and the internal pore material has not been fully utilized; at the same time, when the temperature is too high, the surface of the particles will produce a local low oxygen and reducing atmosphere, so that the CaS03 has been regenerated. Decomposes into CaO and releases S02, which reduces the utilization of limestone and causes the coking and shutdown of the fluidized bed. Therefore, there is a range of the most desulfurization temperature, which is limited by many factors such as limestone type, particle size, and calcination conditions. At present, the best known desulfurization reaction temperature is between 850°C and 900°C.
Therefore, it is necessary to strengthen the monitoring of the temperature of the material layer in the boiler operation and adjust the temperature of the material layer within the optimum desulfurization reaction temperature range. If the temperature of the material layer exceeds 970T, the amount of coal to be fed shall be appropriately reduced, the amount of primary air shall be increased accordingly, and the amount of return material shall be reduced so that the temperature of the material layer may be lowered; if the temperature of the material layer is lower than 970°C, it shall first be checked whether coal is cut off and appropriate. Increase the amount of coal, reduce primary air volume, increase the amount of return materials, and increase the temperature of the material layer. Once the temperature of the material layer is lower than 700°C, it should be treated with autoclave. It is necessary to ascertain the cause of the temperature decrease and to eliminate it before starting.
The return temperature is the temperature that is returned to the combustion ash by the returner. The CFB bed boiler adopting a high temperature separator has a relatively high returning temperature. Generally, a high material temperature of 20 to 30°C is required to ensure the stable combustion of the boiler and to adjust the combustion. The return temperature must be monitored closely during boiler operation. Excessive temperatures may cause coking in the feeder. Especially in the burning of anthracite, which is more difficult to burn, due to the presence of post-fuel combustion, coking is very difficult due to poor temperature control, and the maximum temperature of the returned material should not exceed 1000°C during operation. The returning temperature can be adjusted by adjusting the coal feeding amount and return air flow rate. If the temperature is too high, the coal feeding amount can be appropriately reduced and the air volume of the returning material can be increased. At the same time, whether or not the feeder is blocked can be checked to ensure the smoothness of the feeder. .
The process flow of the CFB boiler and the requirements of the measured medium determine that the selection of a detection element and the instrument must consider the prevention of blocking and wear. The measurement signal of CFB boiler material layer temperature requires multiple thermocouples to be arranged in the dense layer of the combustion chamber of the furnace. The temperature measurement generally uses a stainless steel sleeve thermocouple as a primary component, and is arranged in the combustion chamber about 200-500 mm from the distribution plate. In the layer, the depth of the furnace wall is 15 to 25mm. The material temperature thermocouple should use the detection element with good stability, responsiveness, wear resistance and low maintenance.
2. The CFB boiler bed temperature in the air volume control system influences the safe continuous operation of the boiler, the desulfurization effect of the boiler and the emission of NOx. A suitable bed temperature can effectively avoid the coking of the hearth, increase the burning rate and the desulfurization rate. From the coupling characteristics of the CFB boiler control parameters, there are many factors affecting the bed temperature, mainly wind, fuel, and limestone. If the bed temperature is adjusted by changing the fuel volume, the boiler main steam pressure fluctuation will inevitably occur at the same time when the bed temperature is adjusted; and changing the limestone amount will cause bed pressure fluctuations and pollutant discharge effects. Therefore, the air volume control system adjustment becomes the main means to control the bed temperature.
The air volume control system mainly includes primary air volume adjustment and secondary air volume adjustment. The primary role of the primary air is to fluidize the bed material in the furnace to give a certain amount of oxygen to the lower dense phase area for fuel combustion. The secondary air mainly adopts upper and lower points. Sectional air supply, the next secondary air is usually sprayed on the upper part of the dense phase area, and the upper secondary air is usually sprayed on the lower part of the dilute phase area to supplement the oxygen required for combustion and reduce the mass concentration of NOx emissions. It acts as a disturbance, strengthens the gas-solid two-phase mixing and changes the temperature concentration distribution of the temperature field and material in the furnace.
The CFB boiler requires more accurate air flow control. The principle of adjusting the air volume is to adjust the secondary air volume accordingly on the premise that the primary air volume meets the fluidization. Because the size of the primary air volume is directly related to the quality of fluidization, the CFB boiler must be subjected to a cold test before operation, and a critical fluidization air volume curve under different material thicknesses (differential pressure of the material layer) should be established. This is used as the lower limit of the air volume adjustment during operation. If the air volume is lower than this value, the material layer may not be well fluidized, and coking will occur when the time is slightly longer. The amount of secondary air is mainly adjusted according to the amount of oxygen contained in the flue gas. Usually, the amount of oxygen after the superheater is used as the standard and is controlled at about 3 to 5%. If the oxygen content is too high, indicating that the air volume is too large, it will increase the boiler heat loss and power plant power consumption; oxygen content is too small will cause incomplete combustion, increase the chemical incomplete combustion loss and mechanical incomplete combustion loss . If the total air volume during operation is not enough, the air volume should be gradually increased to meet the combustion requirements, and the primary and secondary air volume should be continuously adjusted so that the ratio of primary and secondary air flow can reach 5:5 or 6:4. It is best not to use secondary air flow. The air volume is higher than the primary air volume to ensure the normal fluidized state in the hearth and the boiler achieves the best economic performance index. The air volume control diagram is as follows.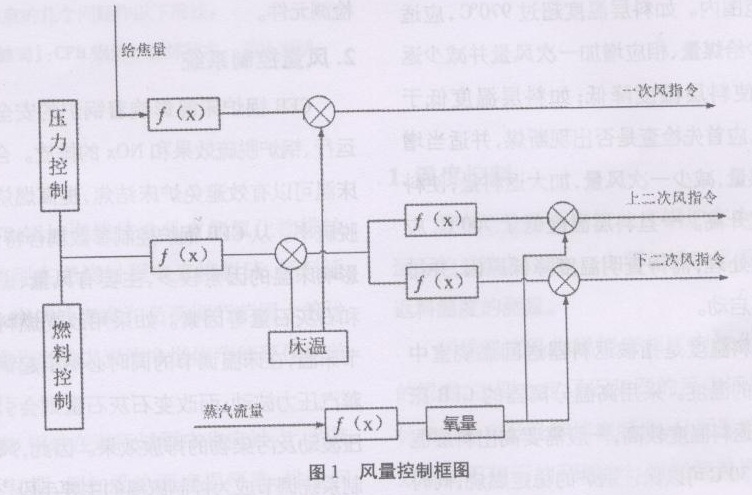
The total air volume command is corrected by the boiler bed temperature after the first and second air volume ratios. The oxygen demand is a function of the steam flow rate of the boiler. The output of the oxygen regulator is modified in two ways to correct the upper and lower secondary air commands. The air volume control system realizes the coordinated control of the boiler air volume and coal volume under the remote control mode to ensure the stability of the pressure, oxygen content and boiler bed temperature under all load conditions.
3. Control of particle size of coal particles In practical operation, the particle size of coal particles plays a decisive role in the combustion of CFB boilers.
1. Effect on the thermal efficiency of the boiler The excessively large particle size of coal particles will affect the full mixing of coal and air, leading to a decrease in the combustion efficiency; more serious is that with the increase in the amount of coal, the large particle size of coal particles will gradually increase, and in the Bed weight deposits form a dead zone, destroying the normal fluidization state, causing uneven furnace temperature field, causing the bed temperature to be too low or bed temperature to coke and forced to stop the furnace; if the coal particles are too fine, then Small coal particles will fly and increase, increasing boiler losses. In severe cases, fine particles will be brought into the separator and returner, causing secondary combustion, causing the coker of the feeder to affect the normal operation of the boiler; Large, too small or even large, will bring difficulties to the operation and operation. At the same time, the heat loss of boiler ash will increase, and the thermal efficiency of the boiler will decrease.
2. Influence on the heating surface of the boiler When the bed temperature is constant, the average diameter of the bed material increases, and the minimum fluidizing air volume required for fluidization of the bed material also increases. Under certain wind pressure, the resistance of the bed material also increases compared to the same. Large, the fluidized state moves in a bad direction, which accelerates the wear of the wind cap on the air distribution plate. At the same time, the fly ash loss increases with the increase of the minimum fluidizing air volume, and the wear of the water wall heating surface increases with the wind speed. Multiplied, resulting in greatly reduced boiler operating cycle.
Therefore, it must be ensured that the size of the coal particles in the furnace is between 1 and 10 mm, and the coal particles with a size of 1 to 10 mm account for more than 65% of the total coal particles.
4. Recycled Material Control CFB boiler's material circulation system plays a decisive role in the safety and stability of the boiler and economic operation. Because in the furnace, the return ash is essentially a heat carrier, which brings the heat in the combustion chamber to the upper part of the furnace, so that the temperature field in the furnace is evenly distributed, and the water wall is exchanged with various heat transfer methods. Therefore, there is a higher heat transfer coefficient (its heat transfer efficiency is about 4 to 6 times that of a pulverized coal furnace). By adjusting the return amount, the temperature of the material layer and the differential pressure of the furnace can be controlled and the boiler load can be further adjusted. On the other hand, the amount of return material has a direct relationship with the separation efficiency of the boiler separation device. The higher the separation efficiency of the separator, the greater the amount of ash in the separated flue gas, and thus the adjustment of the load on the boiler. The larger the operation, the easier it is to operate.
Conclusion In the above aspects, it is necessary to strictly monitor the differential pressure, temperature, furnace differential pressure, and return temperature of the material layer in combination with the conditions of the coal quality and load used during the operation, and continuously adjust the coal supply quantity, air volume, material return quantity, and timely Control the pulverized coal particle size so that the boiler can achieve the best operation effect, minimize the CFB boiler wear and maximize the advantages of CFB boiler energy efficient.
CFB boilers also have shortcomings in the operation process, especially in the initial stage of operation, such as serious abrasion of the heating surface, prominent slagging problems, serious ash leakage in the plenum, and long start-up boiler time. However, as long as the understanding of the characteristics of the circulating fluidized bed technology, to ensure that the boiler design is reasonable, strengthen the equipment management, strengthen the inspection and treatment of the weak links in the boiler, the boiler operation will gradually reach a better level. Based on the investigation of CFB boilers in recent years, we briefly describe the following issues that need to be noted in the boiler combustion control.
1. Temperature control Temperature measurement is one of the key parameters for the safe and stable operation of a circulating fluidized bed boiler, which mainly includes the measurement of the temperature of the material layer and the return temperature.
The temperature of the material layer refers to the temperature of the fluidized material in the combustion dense phase region, which mainly determines the reaction speed, solid product distribution, and pore plugging characteristics of the limestone, thereby affecting the desulfurization efficiency and the utilization rate of the limestone. When the combustion temperature is less than 800°C, the calcining rate of limestone is slowed down, which reduces the surface area available for reaction. As a result, the desulfurization reaction rate decreases, and the effect of limestone capturing SO2 in the bed material deteriorates, making it difficult to achieve effective desulfurization; Below 750T, the desulfurization reaction hardly proceeds anymore, resulting in low-temperature coking and extinguishing. On the other hand, when the combustion temperature is too high (>920°C), the desulfurization efficiency decreases despite the high reaction rate. The reason is that the temperature is too high, it will cause premature blocking of the surface pores of limestone particles, and the internal pore material has not been fully utilized; at the same time, when the temperature is too high, the surface of the particles will produce a local low oxygen and reducing atmosphere, so that the CaS03 has been regenerated. Decomposes into CaO and releases S02, which reduces the utilization of limestone and causes the coking and shutdown of the fluidized bed. Therefore, there is a range of the most desulfurization temperature, which is limited by many factors such as limestone type, particle size, and calcination conditions. At present, the best known desulfurization reaction temperature is between 850°C and 900°C.
Therefore, it is necessary to strengthen the monitoring of the temperature of the material layer in the boiler operation and adjust the temperature of the material layer within the optimum desulfurization reaction temperature range. If the temperature of the material layer exceeds 970T, the amount of coal to be fed shall be appropriately reduced, the amount of primary air shall be increased accordingly, and the amount of return material shall be reduced so that the temperature of the material layer may be lowered; if the temperature of the material layer is lower than 970°C, it shall first be checked whether coal is cut off and appropriate. Increase the amount of coal, reduce primary air volume, increase the amount of return materials, and increase the temperature of the material layer. Once the temperature of the material layer is lower than 700°C, it should be treated with autoclave. It is necessary to ascertain the cause of the temperature decrease and to eliminate it before starting.
The return temperature is the temperature that is returned to the combustion ash by the returner. The CFB bed boiler adopting a high temperature separator has a relatively high returning temperature. Generally, a high material temperature of 20 to 30°C is required to ensure the stable combustion of the boiler and to adjust the combustion. The return temperature must be monitored closely during boiler operation. Excessive temperatures may cause coking in the feeder. Especially in the burning of anthracite, which is more difficult to burn, due to the presence of post-fuel combustion, coking is very difficult due to poor temperature control, and the maximum temperature of the returned material should not exceed 1000°C during operation. The returning temperature can be adjusted by adjusting the coal feeding amount and return air flow rate. If the temperature is too high, the coal feeding amount can be appropriately reduced and the air volume of the returning material can be increased. At the same time, whether or not the feeder is blocked can be checked to ensure the smoothness of the feeder. .
The process flow of the CFB boiler and the requirements of the measured medium determine that the selection of a detection element and the instrument must consider the prevention of blocking and wear. The measurement signal of CFB boiler material layer temperature requires multiple thermocouples to be arranged in the dense layer of the combustion chamber of the furnace. The temperature measurement generally uses a stainless steel sleeve thermocouple as a primary component, and is arranged in the combustion chamber about 200-500 mm from the distribution plate. In the layer, the depth of the furnace wall is 15 to 25mm. The material temperature thermocouple should use the detection element with good stability, responsiveness, wear resistance and low maintenance.
2. The CFB boiler bed temperature in the air volume control system influences the safe continuous operation of the boiler, the desulfurization effect of the boiler and the emission of NOx. A suitable bed temperature can effectively avoid the coking of the hearth, increase the burning rate and the desulfurization rate. From the coupling characteristics of the CFB boiler control parameters, there are many factors affecting the bed temperature, mainly wind, fuel, and limestone. If the bed temperature is adjusted by changing the fuel volume, the boiler main steam pressure fluctuation will inevitably occur at the same time when the bed temperature is adjusted; and changing the limestone amount will cause bed pressure fluctuations and pollutant discharge effects. Therefore, the air volume control system adjustment becomes the main means to control the bed temperature.
The air volume control system mainly includes primary air volume adjustment and secondary air volume adjustment. The primary role of the primary air is to fluidize the bed material in the furnace to give a certain amount of oxygen to the lower dense phase area for fuel combustion. The secondary air mainly adopts upper and lower points. Sectional air supply, the next secondary air is usually sprayed on the upper part of the dense phase area, and the upper secondary air is usually sprayed on the lower part of the dilute phase area to supplement the oxygen required for combustion and reduce the mass concentration of NOx emissions. It acts as a disturbance, strengthens the gas-solid two-phase mixing and changes the temperature concentration distribution of the temperature field and material in the furnace.
The CFB boiler requires more accurate air flow control. The principle of adjusting the air volume is to adjust the secondary air volume accordingly on the premise that the primary air volume meets the fluidization. Because the size of the primary air volume is directly related to the quality of fluidization, the CFB boiler must be subjected to a cold test before operation, and a critical fluidization air volume curve under different material thicknesses (differential pressure of the material layer) should be established. This is used as the lower limit of the air volume adjustment during operation. If the air volume is lower than this value, the material layer may not be well fluidized, and coking will occur when the time is slightly longer. The amount of secondary air is mainly adjusted according to the amount of oxygen contained in the flue gas. Usually, the amount of oxygen after the superheater is used as the standard and is controlled at about 3 to 5%. If the oxygen content is too high, indicating that the air volume is too large, it will increase the boiler heat loss and power plant power consumption; oxygen content is too small will cause incomplete combustion, increase the chemical incomplete combustion loss and mechanical incomplete combustion loss . If the total air volume during operation is not enough, the air volume should be gradually increased to meet the combustion requirements, and the primary and secondary air volume should be continuously adjusted so that the ratio of primary and secondary air flow can reach 5:5 or 6:4. It is best not to use secondary air flow. The air volume is higher than the primary air volume to ensure the normal fluidized state in the hearth and the boiler achieves the best economic performance index. The air volume control diagram is as follows.
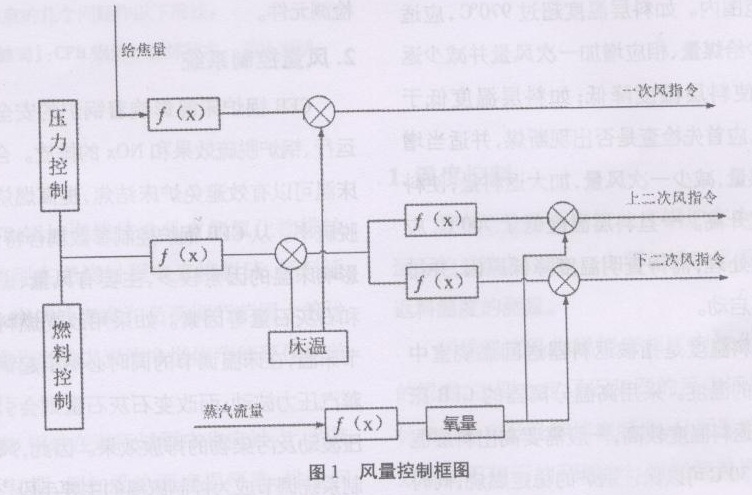
The total air volume command is corrected by the boiler bed temperature after the first and second air volume ratios. The oxygen demand is a function of the steam flow rate of the boiler. The output of the oxygen regulator is modified in two ways to correct the upper and lower secondary air commands. The air volume control system realizes the coordinated control of the boiler air volume and coal volume under the remote control mode to ensure the stability of the pressure, oxygen content and boiler bed temperature under all load conditions.
3. Control of particle size of coal particles In practical operation, the particle size of coal particles plays a decisive role in the combustion of CFB boilers.
1. Effect on the thermal efficiency of the boiler The excessively large particle size of coal particles will affect the full mixing of coal and air, leading to a decrease in the combustion efficiency; more serious is that with the increase in the amount of coal, the large particle size of coal particles will gradually increase, and in the Bed weight deposits form a dead zone, destroying the normal fluidization state, causing uneven furnace temperature field, causing the bed temperature to be too low or bed temperature to coke and forced to stop the furnace; if the coal particles are too fine, then Small coal particles will fly and increase, increasing boiler losses. In severe cases, fine particles will be brought into the separator and returner, causing secondary combustion, causing the coker of the feeder to affect the normal operation of the boiler; Large, too small or even large, will bring difficulties to the operation and operation. At the same time, the heat loss of boiler ash will increase, and the thermal efficiency of the boiler will decrease.
2. Influence on the heating surface of the boiler When the bed temperature is constant, the average diameter of the bed material increases, and the minimum fluidizing air volume required for fluidization of the bed material also increases. Under certain wind pressure, the resistance of the bed material also increases compared to the same. Large, the fluidized state moves in a bad direction, which accelerates the wear of the wind cap on the air distribution plate. At the same time, the fly ash loss increases with the increase of the minimum fluidizing air volume, and the wear of the water wall heating surface increases with the wind speed. Multiplied, resulting in greatly reduced boiler operating cycle.
Therefore, it must be ensured that the size of the coal particles in the furnace is between 1 and 10 mm, and the coal particles with a size of 1 to 10 mm account for more than 65% of the total coal particles.
4. Recycled Material Control CFB boiler's material circulation system plays a decisive role in the safety and stability of the boiler and economic operation. Because in the furnace, the return ash is essentially a heat carrier, which brings the heat in the combustion chamber to the upper part of the furnace, so that the temperature field in the furnace is evenly distributed, and the water wall is exchanged with various heat transfer methods. Therefore, there is a higher heat transfer coefficient (its heat transfer efficiency is about 4 to 6 times that of a pulverized coal furnace). By adjusting the return amount, the temperature of the material layer and the differential pressure of the furnace can be controlled and the boiler load can be further adjusted. On the other hand, the amount of return material has a direct relationship with the separation efficiency of the boiler separation device. The higher the separation efficiency of the separator, the greater the amount of ash in the separated flue gas, and thus the adjustment of the load on the boiler. The larger the operation, the easier it is to operate.
Conclusion In the above aspects, it is necessary to strictly monitor the differential pressure, temperature, furnace differential pressure, and return temperature of the material layer in combination with the conditions of the coal quality and load used during the operation, and continuously adjust the coal supply quantity, air volume, material return quantity, and timely Control the pulverized coal particle size so that the boiler can achieve the best operation effect, minimize the CFB boiler wear and maximize the advantages of CFB boiler energy efficient.
Marco Lift (Ningbo) Co., Ltd. , https://www.marcolift-asia.com