Phone Accessories Finished by Metal Injection Molding Tec
Fortunately, there are several parts of design such as hinges, fiber optic connector bases, and new style connectors are closely dependent on MIM technology. These products are being produced in a large number and MIM technology is being adopted by more and more.
MIM and CIM--Drome can provide one-stop service solution.
The basic attributes include:
1.Economical production of complex parts with weight from 0.03 to 200g from high-performance engineering materials.
2.Parts with high dimensional precision (±0.1%~±0.5%) and good surface quality (surface roughness 1~2μm).
3.Parts with high relative density (96%~100%), homogeneous microstructure and superior performance.
4.Adaptable to powders of various materials and wide application of the parts.
5.Material saving through the recycle of wastes, production process with high level of automation and suitable for mass production
Flow chart of metal injection molding
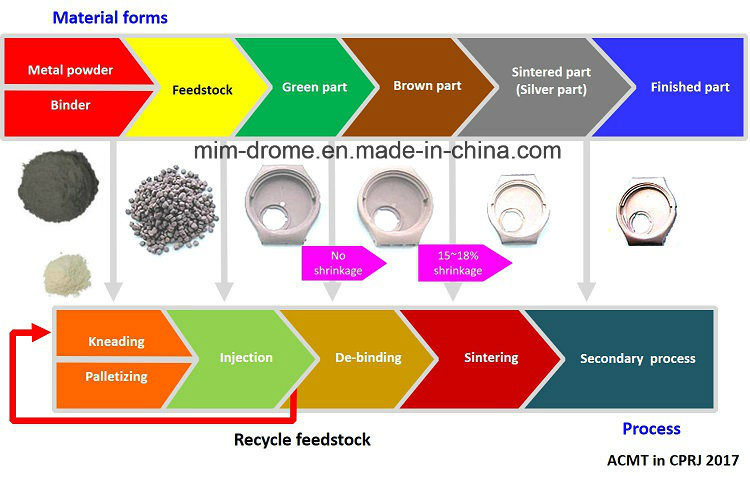
Application of MIM
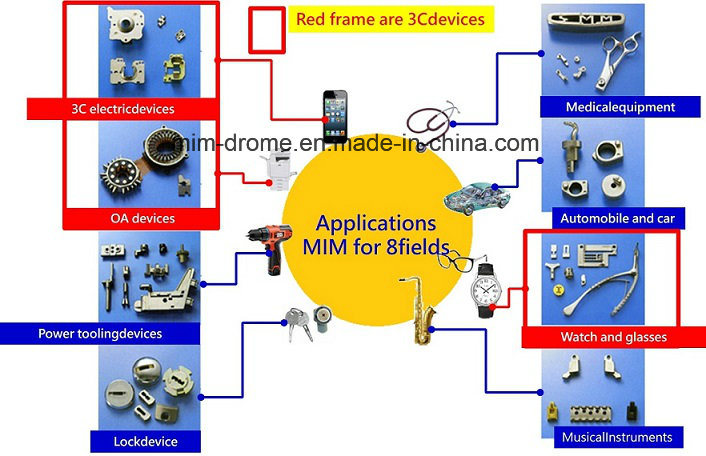
Products Range:
Â
Material | Â | Typical Values | Â | Â | ||||
Designation Code | Density g/cm3 | Tensile Properties | Young's modulus, Gpa | Un-notched Charpy Impact Energy,J | Hardness,Rockwell | |||
 |  | UTS. Mpa | Y.S. (0.2%), Mpa | Elongation (in 25.4mm) % |  |  | Macro (apparent) |  Micro (converted) |
MIM-Fe2Ni | 7.8 | 280 | 115 | 25 | Â | Â | 55 HRB | 50HRCÂ Â Â Â |
MIM-Fe8Ni | 7.8 | 450 | Â | 12 | Â | Â | 84HRB | 50HRCÂ Â Â Â |
MIM-2200 (as sintered) | 7.8 | 290 | 125 | 40.0 | 190 | 135 | 45 HRB | Â |
MIM-2700 (as sintered) | 7.8 | 415 | 255 | 26.0 | 190 | 175 | 69 HRB | Â |
MIM-4605 (as sintered) | 7.8 | 440 | 205 | 15.0 | 200 | 70 | 62 HRB | Â |
MIM-4605 (Q&T) | 7.8 | 1655 | 1480 | 2.0 | 205 | 55 | 48 HRC | 55 HRC |
MIM-304L | 7.8 | 500 | Â | 70 | Â | Â | 60 HRB | Â |
MIM-316L (as sintered) | 7.85 | 520 | 175 | 50.0 | 190 | 190 | 67 HRB | Â |
MIM-410 | 7.7 | 900 | Â | 7 | Â | Â | Â | 40 HRC |
MIM-420 (heat treated) | 7.7 | 1380 | 1200 | 12 | 190 | 40 | Â | 45-60HRC |
MIM-430L (as sintered) | 7.8 | 410 | 240 | 25.0 | 210 | 150 | 65 HRB | Â |
MIM-440C | 7.8 | 700 | 590 | 15 | Â | Â | Â | 45-60HRC |
MIM-17-4PH (as sintered) | 7.8 | 900 | 730 | 6.0 | 190 | 140 | 27 HRC | Â |
MIM-17-4PH (heat treated) | 7.8 | 1190 | 1090 | 6.0 | 190 | 140 | 33 HRC | 40 HRC |
Material | Density( g/m 3) | Tensile Strength( Mpa) | elastic modulus( Gpa) | (thermal conductivity) W/(mk) | ( Thermal Expansion) 10-6/k |
Copper(Cu) | 8.9 | 100 | 130 | 250 | 13 |
Invar(fe-36ni) | 8 | 300 | 205 | 20 | 5 |
Kovar Or F15 (Fe-29ni-17co) | 8.0 | 480 | 200 | 17 | 4.9 |
 Molybdenum-copper (Mo-15cu) | 10 | 210 | 280 | 170 | 7 |
 Molybdenum-copper (Mo-20cu) | 9.9 | 200 | 280 | 145 | 6.5 |
 Tungsten-copper (W-10cu) | 17 | 500 | 340 | 209 | 6 |
 Tungsten-copper (W-20cu) | 16 | 560 | 290 | 247 | 7 |
 Tungsten-copper (W-30cu) | 14 | 420 | 260 | 260 | 11 |
product field
Â
Aerospace | Airfoil Hinge,Rocket Nozzle,Guided Missile Spoiler,Turbine Blade Core |
Auto Industry | Ignittion Control Lock Parts,Turbo Charger Rotor,Valve Guide Rail,Break Gear Parts and Sun Block Shack Parts |
Electronics | Disc drive parts,Cable Connector,Electronic Valve Shell,Computer Print Head,Electronic Packaging Parts and Heat Sink Material |
War Industry | Mine Rotor,Gun Trigger,Armor Piercer,Sight Base,Flechette Arrow and Shrapnel |
Medical Industry | Orthopaedic Bracket,Internal Sewing Needle,Biopsy Forceps,Radiation-proof Cover |
Daily Necessities | Watch Shell,Watch Belt,Watch Buckle,Golf head and Ball Seat,Sport Shoe-buckle,PE Mechanical Parts,Hole Puncher,Fish Catch and Bias Hammer |
Mechanical Industry | Irregular Milling Cutter,Cutting Tools,Micro Gears and Sewing Machine Parts |
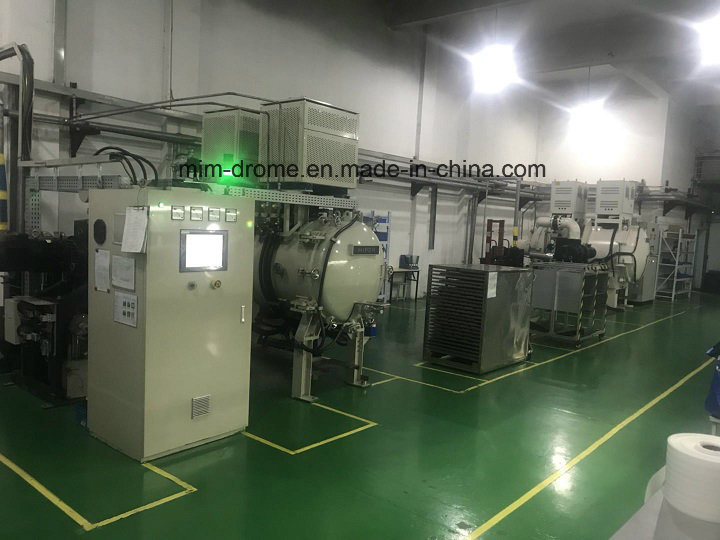
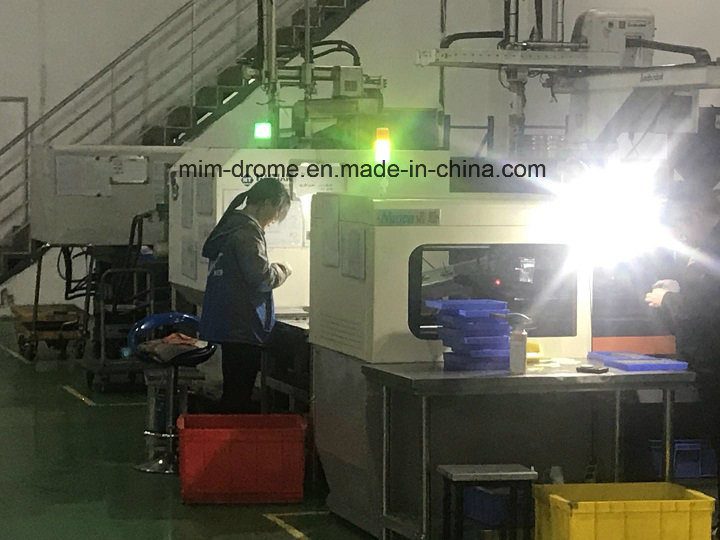
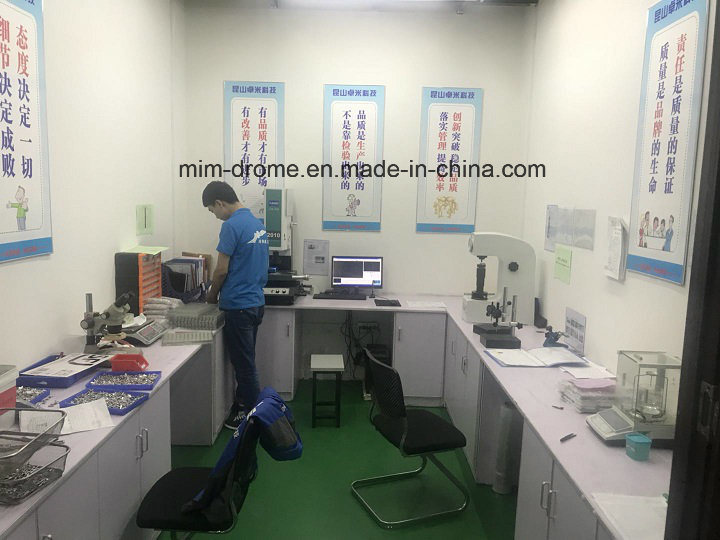
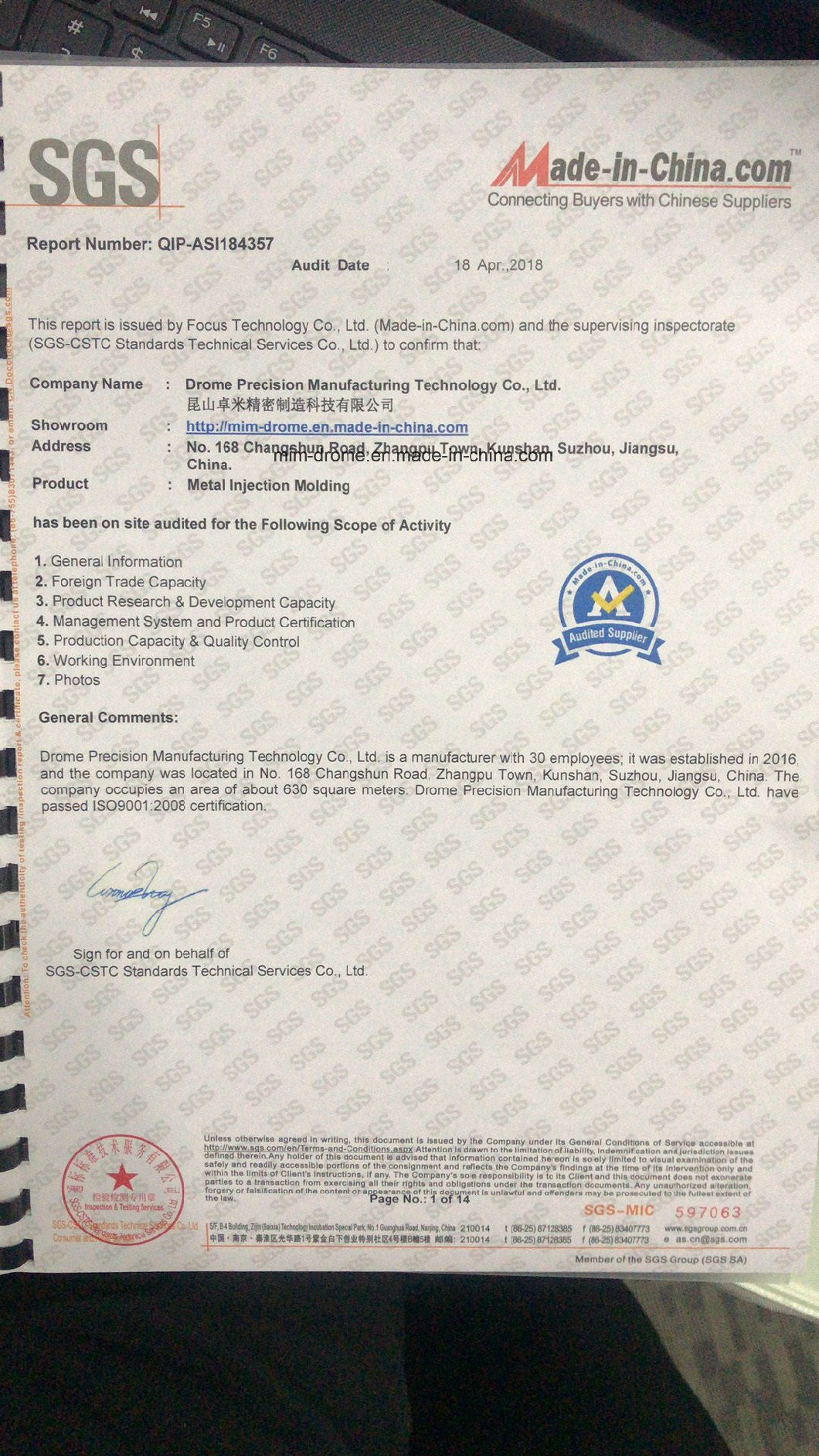
FAQ
1.How can I give you an offer?
Please send us product 2D/3Ddrawings.
PROCESS
Customer Inquiry →Engineering Communication →Cost Analysis →Sales Analysis →Quote to Customer
» 1 Work Days Only
» Submit RFQ with complete commercial terms
  Â
2. How to transport?
For small quantity, we choose TNT, FEDEX, UPS etc
For big quantity, air or sea would be available .
Â
3. packing details?
We attached our normal packing details Plastic disc/carton.
If the customer has specified packing specification, we will pack according to the customer's requirement.
Company Profile
- Design and manufacture Metal Injection Molding Parts, Ceramic Injection Molding Parts, Plastic Injection Molding Parts
- Current 10,000 Manufacturing Space, 30,000 in Construction;
- More than 200Â Employees, 17 Engineers;
- 2017 Sales Revenue >10 Million USD;
- IATF 16949, ISO 9001, OHSAS 18001, ISO 14001;
- 5% Revenue Yearly Invested in R&D;
- Best Machines, Germany Arburg, Japan Nissei, Japan Shimadzu;etc.;
- Serving Top Players in Industries of Auto, Consumer Electronics, Medical Appliance, etc. ;
Â
Chromium carbide thermal spray powder is a type of coating material used in thermal spray processes. It is composed of chromium and carbon, with the chemical formula Cr3C2.
This powder is commonly used in applications where high wear resistance and hardness are required. It is often applied as a protective coating on surfaces that are subjected to abrasive or erosive environments, such as industrial equipment, cutting tools, and engine components.
The thermal spray process involves heating the powder to its melting point and then propelling it onto the surface to be coated using a high-velocity gas or plasma stream. Upon impact, the molten particles solidify and bond with the substrate, forming a dense and durable coating.
The chromium carbide coating provides excellent resistance against wear, corrosion, and oxidation. It also exhibits good adhesion to various substrates, including metals, ceramics, and composites. Additionally, it has a low coefficient of friction, making it suitable for applications where reduced friction and improved sliding properties are desired.
Overall, chromium carbide thermal spray powder is a versatile and effective coating material that offers superior protection and performance in demanding industrial applications.
HVOF Powder,Chromium Carbide Powder,Chromium Carbide Coating,Chromium Carbide Thermal Spray Powder
Luoyang Golden Egret Geotools Co., Ltd , https://www.xtcmetalpowder.com