Maintenance efficiency of mobile smart meters
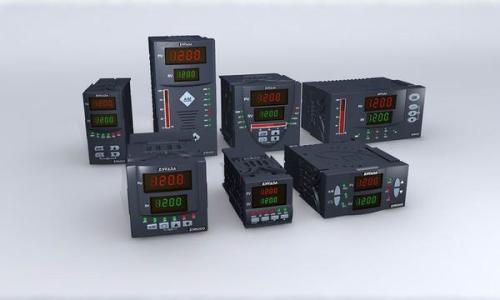
Simplify Circuit Design Principles Simplify function design and simplify circuit design to facilitate inspection, analysis, judgment, and troubleshooting in the maintenance of portable smart instruments. On the other hand, simplifying the circuit design and implementing the instrument function with software as much as possible can greatly reduce the production cost of portable intelligent instruments, effectively increase the reliability of the instrument and reduce the failure. Therefore, the simplified circuit design can reduce the maintenance time and maintenance costs of the product and enhance the maintainability of the instrument.
Maintenance accessibility design principle The so-called maintenance accessibility refers to the ability to quickly and easily achieve the characteristics of the maintenance site during product maintenance. Portable smart devices are compact and lightweight, compact in structure, and perform clever and rational structural design, making it easy to inspect, assemble, and dismantle instruments, and to maintain quickly. Therefore, maintenance accessibility design is a product design consideration.
Design principles of easy-to-change consumables Although portable smart instruments use high-reliability components in their designs, due to the effects of longevity and harsh environments, parts of the instruments are still consumable parts, requiring frequent replacement. . In the product design, the battery, safety tube and other consumables should try to use the cover outside the casing installation method, so that the wearing parts do not have to open the instrument casing, easy to replace.
Maintainability Design Method Hardware Maintainability Design Method
1. Reasonable selection of components Portable intelligent instruments are mainly used for production, scientific research, inspection, trade site, usually using commercially available dry battery power supply. The selection of commercially available dry batteries should consider two factors: first, the volume and capacity ratio of the battery; second, the battery is easy to purchase and easy to replace. In general, the portable smart instrument can be powered by the No. 5 battery. In order to facilitate maintenance and replacement, the resistance and capacitance components of each unit circuit of the portable intelligent instrument should use metal film resistors (RJ), ceramic capacitors, mica monolithic capacitors and aluminum electrolytic capacitors as far as possible. In addition to the calibration circuit, the circuit design of portable smart instruments should use fixed resistors instead of trimmer potentiometers.
The integrated operational amplifier should have a certain working margin and use a single power supply. The connector is used as little as possible, and the connection between the separate parts can be wire bonding. The monitor should use a liquid crystal display (LCD), which is connected to the drive circuit using conductive rubber. Microcontrollers should select devices that are small in size, low in power consumption, and conducive to anti-jamming design.
2. Set up the instrument fault self-test function According to the electrical characteristics of each signal channel, through the hardware and software methods, realize the fault self-diagnosis of portable intelligent instruments. Displaying the instrument's fault self-diagnostics information on the instrument's display helps the maintenance personnel and instrument users quickly and accurately identify the instrument's faults, thereby quickly troubleshooting and effectively improving the repair speed.
3. Reserve test points When designing the printed circuit board of the instrument, test points should be set in each signal path according to the operating characteristics of the instrument circuit so as to facilitate maintenance personnel to observe the signal and quickly determine the fault location. The test point should be reserved for ease of maintenance.
If conditions permit, it is also possible to print the voltage value or waveform of the test point beside the reserved test point. High-pressure dangerous parts should have obvious warning signs. Marks, data, and graphics of the test points should be printed in a position easily visible by maintenance personnel.
Single blanks are employed to produce parts
or products with deeper shapes. Throughout the Deep Drawing process a metal
blank is shaped via pressure applied by a metal die. The process could stamp
and form stainless steel, brass, bronze, cold rolled steel, aluminum, copper
etc.
Milk bucket is one of the many products
made by deep drawing process. The deep draw process begins with metal blanks. It
could be produced into various capacity, dimension, thickness and surface color.
MSG has more than 10 years of experience in
Sheet Metal Fabrication, deep drawing processing. We`re glad to offer
professional OEM service and technical assistance for you.
Huiye Hardware & Electrical Equipment Company Ltd. , https://www.huiyehardware.com