Laser Grating Doppler Transverse Displacement Telemetry Sensor
1 Overview
In recent years, many scientific researchers at home and abroad have devoted laser speed measurement technology to displacement measurement. Such as the West Germany Institute of Physics and Technology successfully developed a method without contact online measurement length [1], can give 818 pulses in 1mm length (movement direction and beam angle of 75 °) when the angle becomes smaller pulse number decreases When the included angle is zero, it cannot work, so it is not convenient to use due to the unstable counting equivalent. The Xiamen Institute of Electronic Science and Technology of China uses the principle of Doppler to measure the length. The measurement range is from 2mm to 10m, the minimum display value is 1mm, and the accuracy is 0.1% [2]. The above method uses scattered light for non-contact measurement. The measured motion and the laser beam are close to perpendicular. This feature is different from the interferometer and laser vibrometer, so it is called a “transverse sensorâ€. For general scatterers, due to weak scattered light signals on the surface, low signal-to-noise ratio, and signal fluctuations caused by scatterer surface texture factors, sometimes signal flooding or signal discontinuity may affect the measurement accuracy. So the current resolution that can be achieved is 10 More than m, affect the promotion and application of this technology, the fundamental reason is from the laser, modulator, the external environment caused by interference and noise.
This article describes a grating lateral displacement telemetry sensor. It is measured using the Doppler effect of the diffraction grating. The resulting Doppler signal has nothing to do with the wavelength of the light. It is determined only by the grating constant. The signal is strong, the signal to noise ratio is high, and the anti-interference ability is strong. The measurement system is simplified. In addition, due to the periodic structure of the grating, the generated beat signal is a continuous sine wave, which relieves the burden of the signal processing system, thereby obtaining high resolution and easy realization of high-precision displacement telemetry. Due to the improvement of signal-to-noise ratio, phase measurement is realized, detection distance is 2 to 50m, and spatial resolution is 0.4. m, 10 to 100 times more than the usual Doppler technology. An acousto-optic modulator was introduced in the differential optical system to perform splitting and frequency shifting to realize the discrimination.
2 Measurement principle
The Doppler effect refers to the wave frequency variation caused by the relative motion between the wave source, receiver, propagation medium, or intermediate reflector. The formula is approximately:
(1)
Where f0—light frequency emitted by the light source;
F—the frequency of the light received by the receiver;
V—The relative movement speed between the light source and the receiver takes '+' when they are close to each other and '-' when they are far away;
U—the speed of light in the medium; - The angle between the line direction of the light source and the receiver and the direction of the speed.
If the grating is used as a moving body, as shown in Fig. 1, the main diffraction The frequency shift in the angular direction is:
(2)
Fig. 1 The grating Doppler effect
Where i-parallel light incident angle; - diffraction angle;
V-grating motion speed; - Optical wavelength,
The grating equation d(sini±sin )=k
Substitute the above equation to get the grating Doppler formula:
(3)
Where k-diffraction orders;
d - grating constant; fk—The frequency shift value corresponding to the k-th order diffraction principal maxima.
It can be seen from the formula (3) that when the grating is moving, the Doppler shift of the diffracted beam is independent of the incident angle and the incident light wavelength, and is only related to the diffraction order, the grating movement speed, and the grating pitch. The zero-order diffracted light has no frequency shift, and the first-order diffracted light has a frequency shift of F1=V/d,
F-1=-V/d.
For reflective gratings, it has the following properties:
1 The zero-order diffracted light is in the reflection direction, and the Doppler shift is zero, as shown in Fig. 2(a);
(2) When the light is perpendicularly incident, the ±1st-order diffracted light is separated on both sides of the normal line, and the angle is the same as the normal line. , see Figure 2(b);
(3) If the light is incident in -1 order from 2(b), the direction of the vertical grating plane is +1 order diffracted light, and the frequency shift is: F1=V/d, the zero order is in the reflection direction; conversely, if it is incident from the +1 order direction in 2(b), the direction of the vertical grating plane is -1 order diffracted light, and the frequency shift is:
F-1=-V/d, see Fig. 2(c), 2(d).
Fig. 2 Doppler frequency shift characteristics of reflective grating
When the two beams are respectively incident from the directions shown in Figs. 2(c) and (d), the optical element is properly adjusted so that the diffraction +1 order main maxima in (c) and (d) in the mixing beat Diffraction - 1 orders are mostly coincident, and return along the optical axis, then the frequency difference after mixing the two diffracted lights is:
(4)
For the cumulative pulse count of this beat signal, the grating displacement x is obtained:
(5)
(6)
Equation (6) gives the theoretical basis for lateral displacement measurement using the Doppler effect of a moving grating. The discrimination of displacement direction is achieved by a method of prefabricated frequency shift. This system adopts the acousto-optic modulator to achieve the purpose of splitting and prefabricating the frequency shift, and it can also effectively suppress the optical feedback. When the laser beam is incident on the acousto-optic device as it is incident on the moving phase grating, acousto-optic diffraction occurs and a frequency shift occurs. When incident at Bragg angle, the diffracted beam will focus only on zero-shift and frequency shift 1st-order diffracted light with a constant frequency difference between the two
(
For the frequency of ultrasound).
3 grating lateral displacement telemetry sensor structure
3.1 Optical system Figure 3 shows the optical system of the grating lateral displacement telemetry sensor.
Figure 3 Grating lateral displacement telemetry sensor optical system
The beam of frequency f0 from the laser L is frequency-shifted by the acousto-optic modulator A and divided into frequencies f0 and f0+. For the two beams, since the splitting angle of the acousto-optic device is very small, the prism R and the plane mirror M are combined (for a system with a short measurement distance such as 6m, a combination of a negative lens and a large-aperture imaging lens) to further split the light, The straight system Z collimates the measuring beam on the moving grating G, generates a grating Doppler signal, and takes the +1st order diffraction main maxima and the -1st order diffraction main maximal mixing beats along the optical axis return. The returned beam frequency is
The refraction is reduced by the lens O and the right angle prism T to converge on the photoreceptor E. The application of the collimation system is to reduce the spread of the light beam in the remote measurement.
Since the lateral displacement telemetry sensor adopts a differential optical path structure, influences of external interference signals such as beam drift and additional vibration in long-distance displacement telemetry are effectively eliminated, and the signal-to-noise ratio is greatly improved.
3.2 The frequency of the signal received by the optoelectronic receiver of the signal processing system is After the optical signal is photoelectrically converted, it is divided into two paths, which are respectively different from the phase of the acousto-optic driving power supply
/2 oscillation signal mixing, elimination
, And after low-pass filter amplification, filter high-frequency interference signals and output the same two-way amplitude, phase difference
/2, with Doppler shift
f signal. One of them is inverting, and the difference between the three positions is
The sinusoidal signal of /2 is then finely resolved. Through the reversible counter interfaced with the microcomputer, it is input into the computer for data processing under the control of the program, and the printing result is displayed. The system block diagram is shown in FIG.
Figure 4 grating lateral displacement telemetry sensor signal processing system
4 Experimental studies
4.1 Accuracy comparison experiment In order to estimate the measurement accuracy of the system, a resolution of 1 is used. m grating digital display to compare experiments. In comparison, the digital display meter rod and the measured object (grating) are in the same straight line in order to reduce the impact of Abbe's error. When the measured grating moves, the digital display shows its displacement. At the same time, the computer picks up the counting pulse and displays the printing result after processing. The comparison error is shown in Figure 5.
Figure 5 Comparison experiment results
4.2 Depth-of-Focus Range Experiment Because the intensity of the two beams is not completely equal due to the optical intensity, it is difficult to ensure that the beam accurately overlaps the surface of the grating in long-distance measurements; in addition, the direction of movement during the lateral movement of the grating Axial deviation may also occur if there is an angle with the grating surface. The depth of focus of this system is very large, that is, it is not sensitive to the defocusing of the moving body before and after the intersection point, which makes it very easy to align the target; in addition, the angle (ie tilt) between the grating surface and the moving direction is caused by the movement process. Defocus has also become an insensitive factor. Therefore, the measurement accuracy of the system is not affected within the measured depth of focus.
Figure 6 shows the experimental results of the depth of focus range for different light path configurations.
a Combination of splitting prisms and mirrors (measurement distance is 50m)
b Spectrophotometric combination of negative lens and large aperture imaging lens (measurement distance is 6m)
Figure 6 Depth of focus range experiment results
In the figure, the abscissa indicates the longitudinal displacement of the grating, that is, the displacement of the grating along the optical axis (the lateral displacement of the grating is measured at each position); the ordinate indicates the lateral displacement of the grating, that is, the displacement of the grating along the vertical optical axis (Fig. 6(a) raster moves 1000 each time m, the grating in Figure 6(b) moves 300 each time
m); FL1, FL2 are their focal depth range, respectively.
For the light path structure of different spectroscopic forms, the formula derived by the author's theory is:
1 negative lens and large aperture imaging lens combination:
Laser beam divergence angle =1.3×10-3rad;
Diffraction angle tg ≈0.02;
Laser wavelength =0.6328×10-3mm;
Negative Lens Magnification × Imaging Lens Magnification r1r2 = 2.6.
2 Prism and mirror combination:
Laser beam divergence angle =1.3×10-3rad;
Diffraction angle tg ≈0.02;
Laser wavelength =0.6328×10-3mm;
Collimation System (Inverted Telescope System) Angle of View Magnification =2.5.
The above experimental results show that the lateral displacement telemetry sensor has high measurement accuracy and good repeatability. Through the experiment of focusing depth and the comparison with the theoretical derivation, it can be seen that the system has a large depth of focus range, which makes the defocus of the moving body before and after the intersection point in the displacement telemetry and the angle between the grating surface and the moving direction ( That is, tilting) is not sensitive to defocus caused during the movement and is very easy to align with the target without affecting the measurement accuracy of the system.
5 Concluding remarks
The use of grating Doppler effect for lateral displacement telemetry, with high resolution and measurement accuracy, has great practicality, especially for long-distance high-precision measurement. If the Doppler measurement of general scatterers is further developed, telemetry of deformation of bridges, buildings, etc. can also be realized, which has broad prospects for development.
Fish Farming Aquaculture Drum Filter
The drum filter is mainly composed of four parts: tank component, roller component, backwash component and liquid level automatic control component. It is made of non-toxic seawater corrosion-resistant high-quality engineering plastic materials. A stainless steel filter screen is fixed on the rotatable drum, and the tiny suspended substances in the water are separated and filtered through the screen and finally achieve solid-liquid separation. During the filtering process, small suspended particles in the water will cause the screen to be blocked. When the screen is blocked, the liquid level automatic control component works, and the backwash water pump and roller reducer automatically start working to make the screen timely cleaning to keep the equipment in good working condition.
Our company's drum filter is designed for the problems that the existing filters cannot work automatically, is not resistant to corrosion, the screen is easy to break, easy to block, equipment failure rate is high, and maintenance and operation are difficult. It is one of the solid-liquid separation technologies in the early stage of water treatment in the aquaculture system. This product purifies the water by separating the solid waste in the aquaculture water to achieve the purpose of recycling.
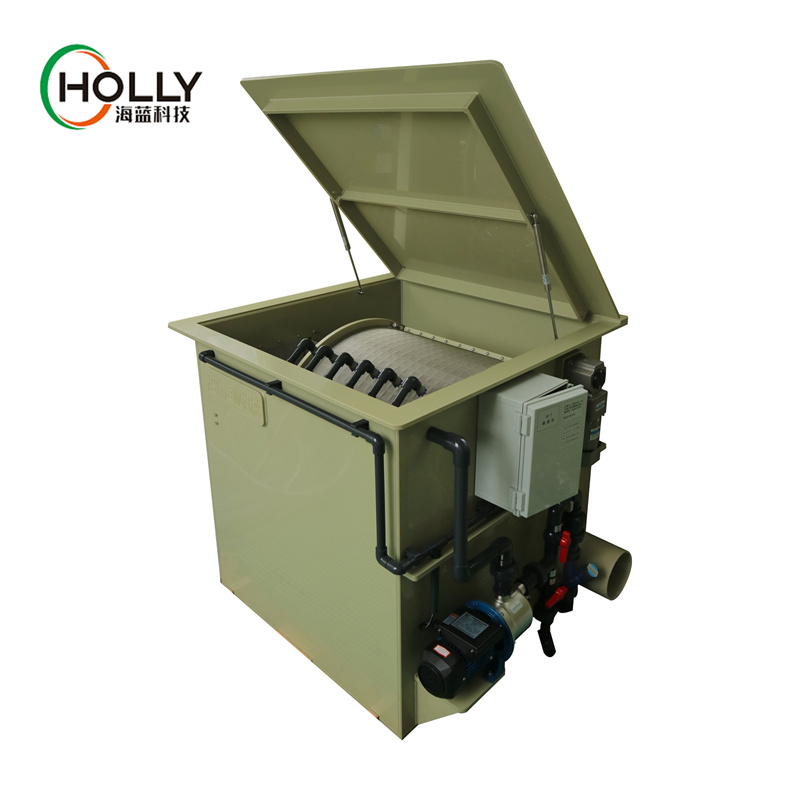
Aquaculture Drum Filter,Fish Farming Drum Filter,Aquaculture Drum Filter Screen,Fish Farming Drum Filter Screen
YIXING HOLLY TECHNOLOGY CO.,LTD. , https://www.watertreatment-machine.com