High-end cutting tool products will win more space for development
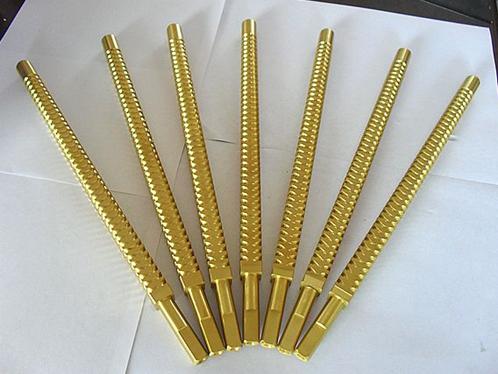
In order to cope with high-speed machining and save a lot of processing time and costs, tool improvement has become an important factor. Due to the higher wear resistance and hardness of tungsten carbide tools, the proportion of tungsten carbide tools in the tool market is increasing. In order to obtain the best benefits in processing, proper surface treatment must be selected. Medium and heavy load molds must be CVD high-temperature titanium plating, supplemented by precision vacuum heat treatment to achieve acceptable deformation. This part is commonly used in cold forging die, hydraulic drawing die, tungsten carbide drawing line, suction pipe. In the application of tools, molds, and mechanical parts with medium or low load or precise requirements, PVD titanium plating at low temperature (150°C to 500°C) is appropriate. Aluminium titanium nitride with high aluminum content can easily form aluminum oxide on the surface of the hard film. This layer of oxide film can make titanium aluminum nitride ceramic hard film oxidation temperature reached 923 degrees Celsius, can protect the high-speed carbide cutting tool edge cutting edge oxidation resistance and maintain high temperature hardness. However, although titanium nitride and titanium carbonitride also form titania oxide films at high temperatures, they are not easily adhered to the hard films and flaking off with chips, which results in the lack of protection of the hard films, rapid oxidation, and deterioration. Therefore, no matter whether the surface treatment of high-temperature or low-temperature coating has to be properly selected, a proper substrate and a stable heat treatment must be selected, supplemented by the pre-treatment of surface fine-grinding and polishing. Ultra-high temperature Resin bond diamond grinding wheel processing efficiency is lower than METROX grinding wheel, due to the high bonding strength of the grinding wheel, the production cycle is short, the processing cost is low, especially when grinding tool edge is not easy to cause chipping, and according to the use requirements, Grinding into a variety of shape and shape of the molding wheel, so it is still widely used in production for a long time. How to further improve the grinding performance of such grinding wheels has also become an important task at present.
With the rapid development of tool design, manufacturing and use technologies, and the ever-increasing output of cutting tools, ultra-high temperature resin-bonded diamond grinding wheels still cannot fully meet the requirements for high-volume production of cutting tools. There is still room for further development in the number and quality of tools. . To this end, Shanghai Zhongyu Company is further studying how to improve the grinding performance of this type of grinding wheel, in particular, a large number of experimental studies have been conducted on the wear resistance of the bonding agent, the bonding strength of the bonding agent and the diamond Abrasive, and the self-sharpening properties. Great progress. The test results show that the improved wheel grinding efficiency can be increased by about 20% on the original basis, and the grinding wheel life can be increased by about 50%.
At present, China's tool production structure and market need to be seriously out of balance. There is a large gap in the market for carbide tools, but the market is now mostly high-speed steel tools and low-end standard tools. Compared with foreign countries, the tool market in China is obviously unbalanced. Manufacturers should adjust tool product transformation as soon as possible and develop high-end, advanced tools.
Chromium(III) sulfate usually refers to the inorganic compounds with the formula Cr2(SO4)3.x(H2O), where x can range from 0 to 18. Additionally, ill-defined but commercially important "basic chromium sulfates" are known. These salts are usually either violet or green solids that are soluble in water. It is commonly used in tanning leather.
Since 33% of the anion charges are due to hydroxy ions the basicity is 33% (but in tanning jargon it is known as 33% reduced). Products with higher basicities, e.g. 42% or 50% may be obtained by the addition of sodium carbonate, these are often used in combination with Sodium Formate. The sodium sulfate is often left in the technical product since it is inert with respect to the tanning process. It is important to fully reduce the hexavalent chromium to trivalent since the hexavalent is more likely to cause health problems for tanners and leather consumers.
Basic Chrome Sulphate,Basic Chrome Sulfate for Tannery,Tanning Agent Basic Chrome Sulfate
HENAN JINHE INDUSTRY CO.,LTD , https://www.hnironoxide.com