Twin Screw Extruder for Color Masterbatch Compounding Pelletizing
Model NO.: ATE Series
Customized: Customized
Certification: CE, ISO9001:2008
Condition: New
Voltage: 380V 50Hz or Customized
Electric Components: ABB,Schneider,Ls,Omron, or Customized
Pelletizing Type: Strand/Underwater Pelletizing
Capacity Range: 40-500kg/H
Trademark: ACERETECH
Transport Package: Wooden Pallet
Specification: CE, TUV
Origin: Jiangsu Zhangjiagang
HS Code: 8477209000
Model NO.: ATE Series
Customized: Customized
Certification: CE, ISO9001:2008
Condition: New
Voltage: 380V 50Hz or Customized
Electric Components: ABB,Schneider,Ls,Omron, or Customized
Pelletizing Type: Strand/Underwater Pelletizing
Capacity Range: 40-500kg/H
Trademark: ACERETECH
Transport Package: Wooden Pallet
Specification: CE, TUV
Origin: Jiangsu Zhangjiagang
HS Code: 8477209000
Twin Screw Extruder for Color Masterbatch Compounding Pelletizing
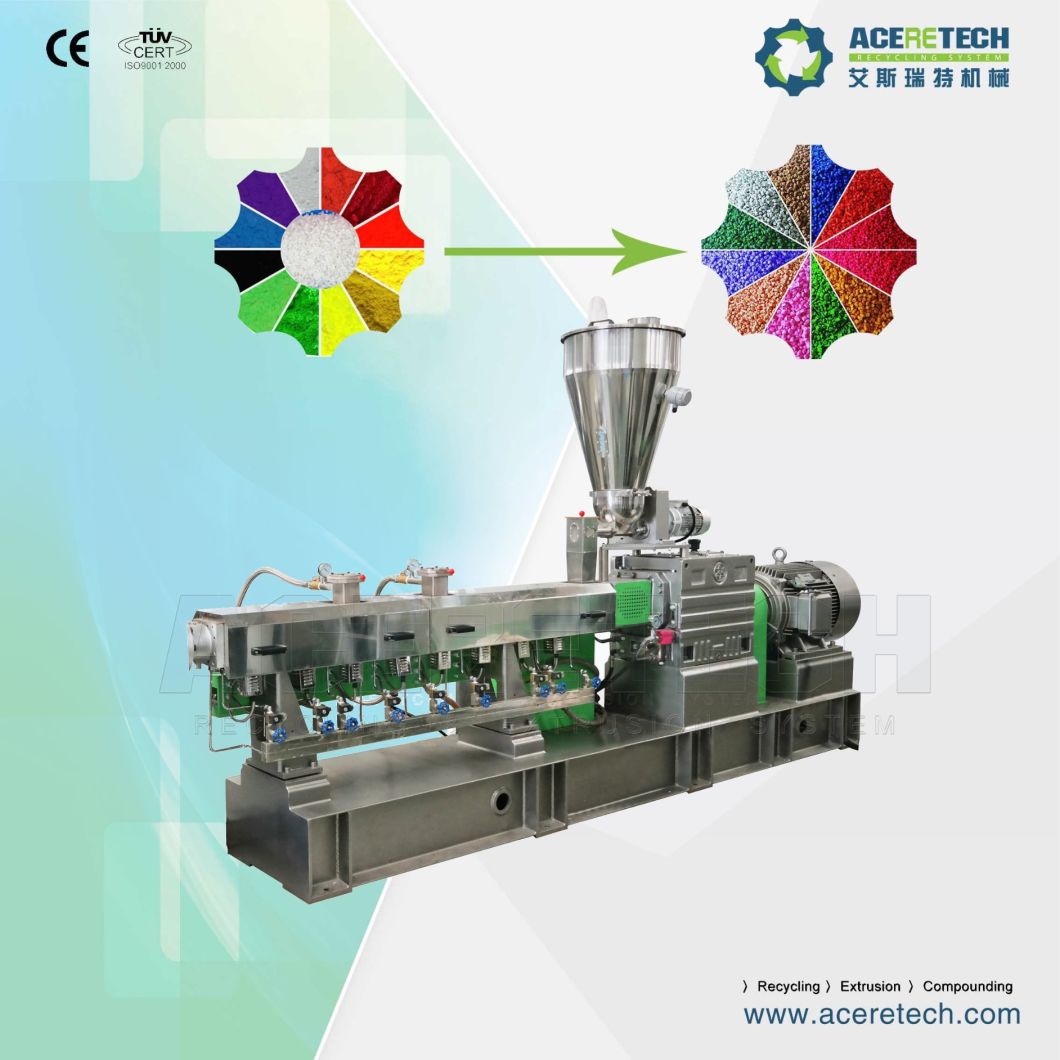
Product description:
Definition of color master batch:
By the high proportion of additives, thermoplastic resin, pigments or the good dispersion of plastic colorants, it chooses the resin of colorants that have good wetting and dispersing effect and good compatibility with being shaded material. It can be explained like: PP/PE/PET/PVC carrier + pigment + additives = color master batch
Generally, we use the special type of extruder to produce this kind of color master batch: ATE Twin Screw Extruder. ATE Series Co-rotating Parallel Twin Screw Extruder consists of motor drive, torque distribution gearbox, processing section, temperature controlling units, die section and down-stream pelletizing system, etc.
Specification:
1.    ATE Series Compounding and Granulating line for Color Master Batch
Process | Color master batch compounding and granulating |
Application | 50-60%PP/PE/PVC/PET, 40%pigment, 8%additives Color Master batch: pigment +additives+ PE/PP/PVC/PETÂ carrier |
Output | 40-500kg/h, depending on the condition of raw Material, formulation and processing, etc. |
NO. | Name |
1 | SHR500A High Speed Mixer |
2 | Screw Loader |
3 | Main feeder |
4 | ATE series Twin Screw Extruder |
5 | Electric Control System(cabinet) |
6 | Strands Pelletizing System/ Under-water Pelletizing System |
7 | Vibrating screen |
8 | Product hopper |
Introduction of parts of ATE Twin Screw Extruder
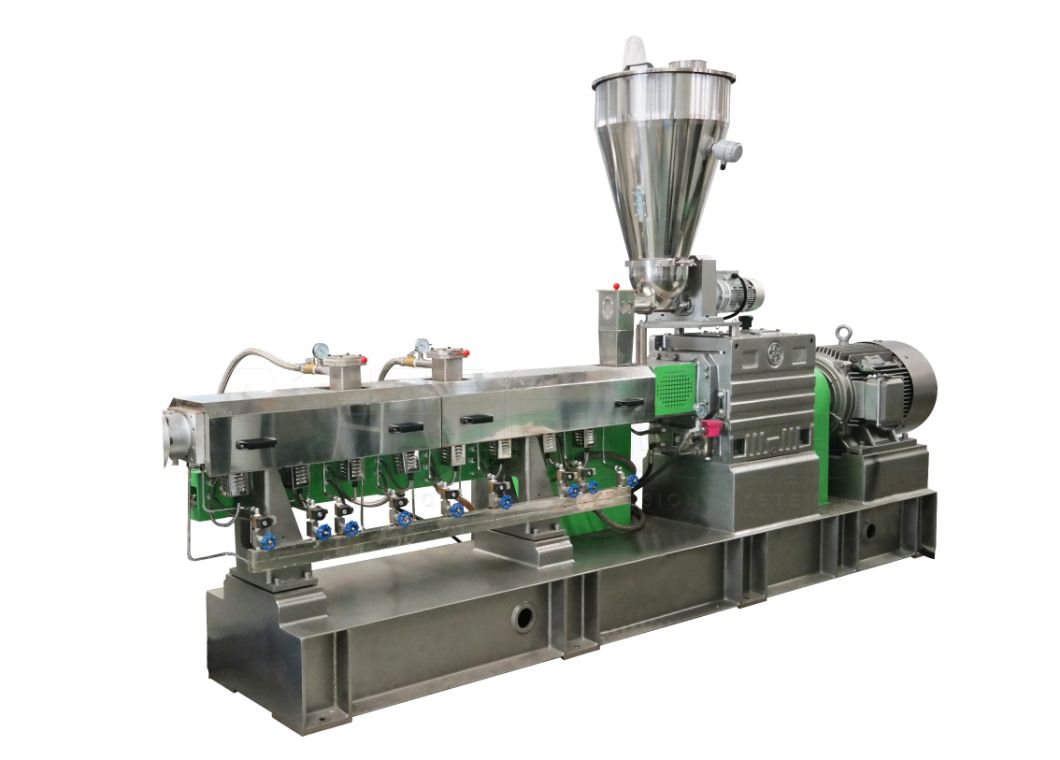
ATE Twin Screw Extruder adopts modular design principle, component standardization manufacturing, which can present stable and reliable performance. Thanks to the modular principle, ATE extruders can provide highly customizable solutions according to customers' process and special requirements. Based on different output torque grade, ATE series extruders have basic type and efficiency type.
Process section includes barrels, screw shafts, screw elements, individual temperature heating and cooling unit. Barrels and screw elements are designed in block principle.
Block structure allows the screw elements combine and sequence optimized to realize the process:
Conveying-Plasticization- Compounding & Dispersion- Homogenization- Degassing- Pressure building
Also Block structure allows the barrels adjust freely to the fit the process requirement.
Based on different process position, ATE extruders have different barrels type: feeding barrel, side feeding barrel, close barrel, open on top barrel, vacuum vent barrel, etc. According to the different jobs' requirement, barrels' materials can be nitride steel or bimetallic steel.
Multiple cutting systems can be combined with ATE Twin Screw Extruder, such as strands pelletizing, hot-face cutting and under-water pelletizing, etc.
Both Instrument control and PLC control are available to apply in the ATE electrical controlling system. All the key electrical parts adopt European brands to guarantee the controlling system with significant and stable performance.
Â
Flow Chart:
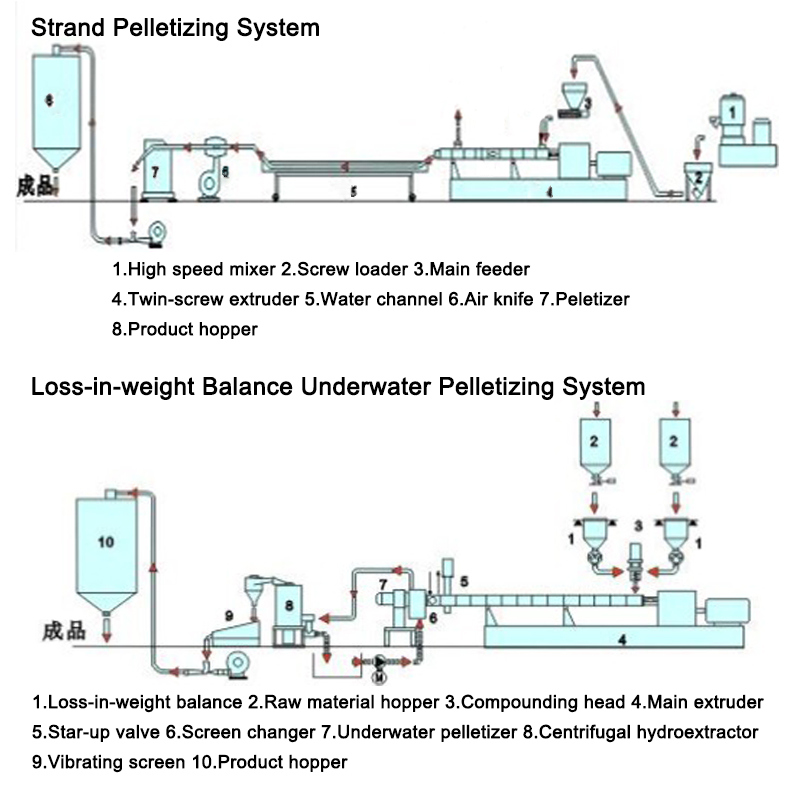
Main technical specification
Machine Size | Screw Diameter(mm) | L/D | Screw Speed Max.(rpm) |
Motor power (Kw) |
Torque per shaft (Nm) |
Specific torque T/A3 |
Throughput rate (kg/h) |
ATE35 | 35.6 | 36-44 | 600 | 15 | 115 | 4.2 | 40-80 |
ATE52 | 51.4 | 36-44 | 600 | 55 | 415 | 5.2 | 120-150 |
ATE65 | 62.4 | 36-44 | 600 | 90 | 675 | 4.8 | 250-350 |
ATE75 | 71 | 36-44 | 600 | 132 | 990 | 4.6 | 350-500 |
Advantages of color master batch:
1. High concentration of pigmentÂ
2. Excellent dispersion, good heat-resistant, high color fastness, stable performance and shows bright color
3. Non-toxic, environmental-friendly
4. Compatible with various material PE/PP/PS/ABS/HIPS/PVC/TPR etc.
5. Wide application: blow moulding, blowing film, injection moulding, extrusion, spin-dyeing, cable sheathing, etc.
6. Range of industrial application: office automation, household appliances, film and packing material, textile, sheet, pipe, medical appliances, toys and so on.
Â
Advantages of the production line
1.    It can produce high-quality, high-quantity filler master batch
2.    It works with high efficiency
3.    It's computerized with high automation
Why choose us
Lower investment cost for a high quality and durable machine;
Low energy consumption with high production output;
Overseas installation and training are available;
Machine warranty with spares in stocking and in-time delivery;
Fast machine delivery and installation: AceRetech produces on an average of 10 sets of plastic machines per month and can deliver the machine faster than most manufacturers. The regular delivery time of an AceRetech recycling machine is 60 days.
Â
Â
Twin Screw Extruder for Color Masterbatch Compounding Pelletizing
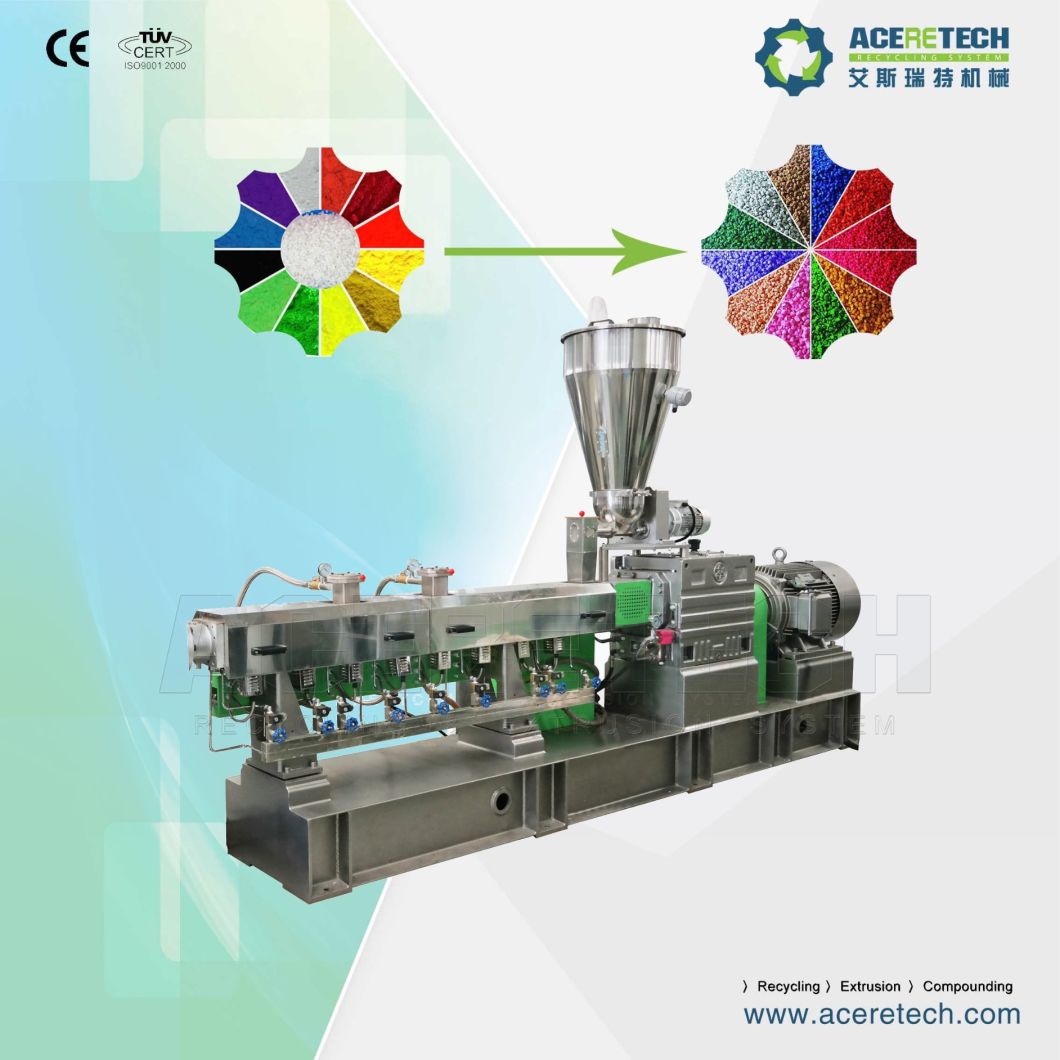
Product description:
Definition of color master batch:
By the high proportion of additives, thermoplastic resin, pigments or the good dispersion of plastic colorants, it chooses the resin of colorants that have good wetting and dispersing effect and good compatibility with being shaded material. It can be explained like: PP/PE/PET/PVC carrier + pigment + additives = color master batch
Generally, we use the special type of extruder to produce this kind of color master batch: ATE Twin Screw Extruder. ATE Series Co-rotating Parallel Twin Screw Extruder consists of motor drive, torque distribution gearbox, processing section, temperature controlling units, die section and down-stream pelletizing system, etc.
Specification:
1.    ATE Series Compounding and Granulating line for Color Master Batch
Process | Color master batch compounding and granulating |
Application | 50-60%PP/PE/PVC/PET, 40%pigment, 8%additives Color Master batch: pigment +additives+ PE/PP/PVC/PETÂ carrier |
Output | 40-500kg/h, depending on the condition of raw Material, formulation and processing, etc. |
NO. | Name |
1 | SHR500A High Speed Mixer |
2 | Screw Loader |
3 | Main feeder |
4 | ATE series Twin Screw Extruder |
5 | Electric Control System(cabinet) |
6 | Strands Pelletizing System/ Under-water Pelletizing System |
7 | Vibrating screen |
8 | Product hopper |
Introduction of parts of ATE Twin Screw Extruder
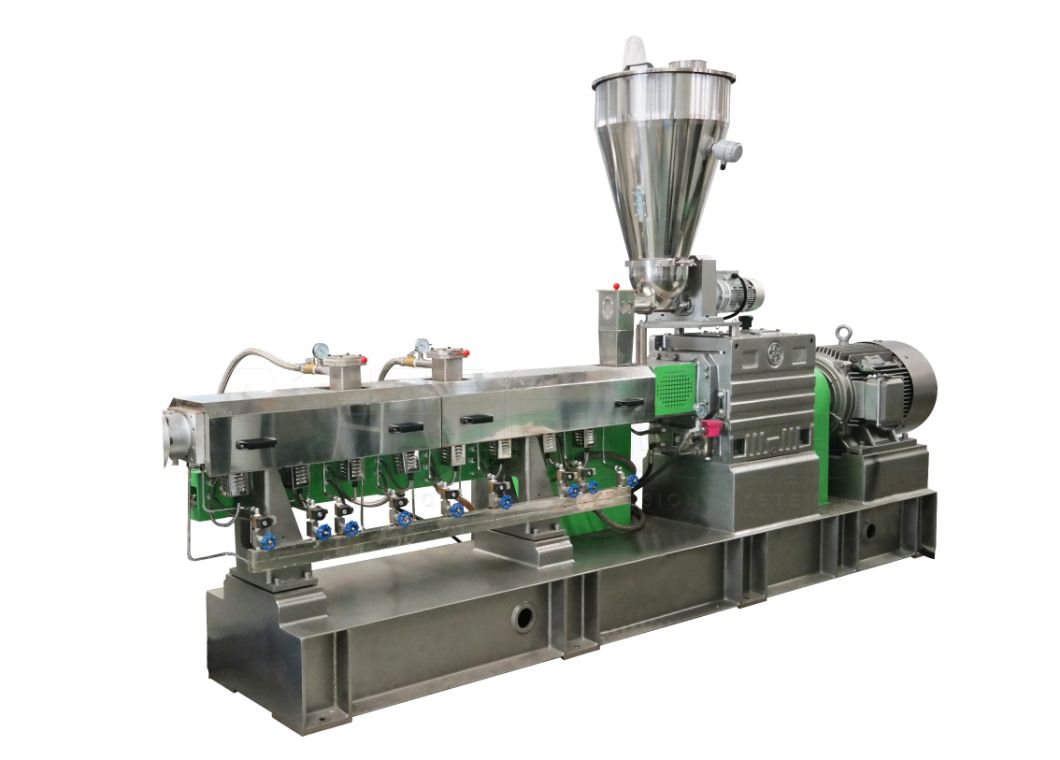
ATE Twin Screw Extruder adopts modular design principle, component standardization manufacturing, which can present stable and reliable performance. Thanks to the modular principle, ATE extruders can provide highly customizable solutions according to customers' process and special requirements. Based on different output torque grade, ATE series extruders have basic type and efficiency type.
Process section includes barrels, screw shafts, screw elements, individual temperature heating and cooling unit. Barrels and screw elements are designed in block principle.
Block structure allows the screw elements combine and sequence optimized to realize the process:
Conveying-Plasticization- Compounding & Dispersion- Homogenization- Degassing- Pressure building
Also Block structure allows the barrels adjust freely to the fit the process requirement.
Based on different process position, ATE extruders have different barrels type: feeding barrel, side feeding barrel, close barrel, open on top barrel, vacuum vent barrel, etc. According to the different jobs' requirement, barrels' materials can be nitride steel or bimetallic steel.
Multiple cutting systems can be combined with ATE Twin Screw Extruder, such as strands pelletizing, hot-face cutting and under-water pelletizing, etc.
Both Instrument control and PLC control are available to apply in the ATE electrical controlling system. All the key electrical parts adopt European brands to guarantee the controlling system with significant and stable performance.
Â
Flow Chart:
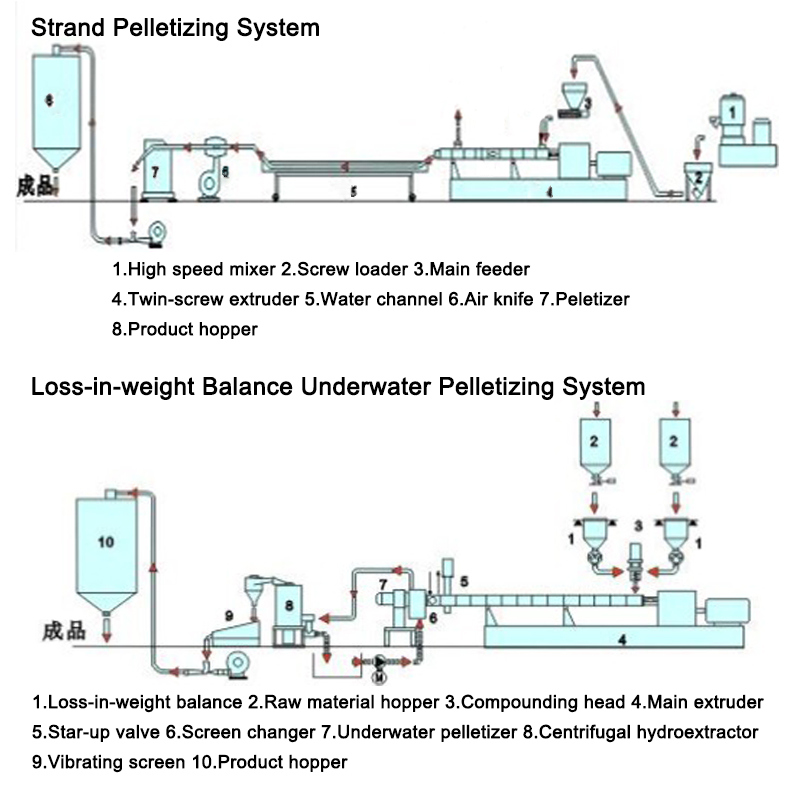
Main technical specification
Machine Size | Screw Diameter(mm) | L/D | Screw Speed Max.(rpm) |
Motor power (Kw) |
Torque per shaft (Nm) |
Specific torque T/A3 |
Throughput rate (kg/h) |
ATE35 | 35.6 | 36-44 | 600 | 15 | 115 | 4.2 | 40-80 |
ATE52 | 51.4 | 36-44 | 600 | 55 | 415 | 5.2 | 120-150 |
ATE65 | 62.4 | 36-44 | 600 | 90 | 675 | 4.8 | 250-350 |
ATE75 | 71 | 36-44 | 600 | 132 | 990 | 4.6 | 350-500 |
Advantages of color master batch:
1. High concentration of pigmentÂ
2. Excellent dispersion, good heat-resistant, high color fastness, stable performance and shows bright color
3. Non-toxic, environmental-friendly
4. Compatible with various material PE/PP/PS/ABS/HIPS/PVC/TPR etc.
5. Wide application: blow moulding, blowing film, injection moulding, extrusion, spin-dyeing, cable sheathing, etc.
6. Range of industrial application: office automation, household appliances, film and packing material, textile, sheet, pipe, medical appliances, toys and so on.
Â
Advantages of the production line
1.    It can produce high-quality, high-quantity filler master batch
2.    It works with high efficiency
3.    It's computerized with high automation
Why choose us
Lower investment cost for a high quality and durable machine;
Low energy consumption with high production output;
Overseas installation and training are available;
Machine warranty with spares in stocking and in-time delivery;
Fast machine delivery and installation: AceRetech produces on an average of 10 sets of plastic machines per month and can deliver the machine faster than most manufacturers. The regular delivery time of an AceRetech recycling machine is 60 days.
Â
Â