Graphene is receiving much attention in the field of lithium battery.
The “green†energy storage and transportation system has become a hot spot in the current energy field. Lithium-ion is one of the important branches, and its performance improvement is the focus of researchers. With the continuous development of research, high-performance lithium battery materials are emerging. In practical applications, the incomplete performance of the prepared materials is the key to restricting their high energy density and high power density. Graphene's high electrical conductivity, high thermal conductivity, high specific surface area, and many other excellent properties have a very important theoretical and engineering value to solve this problem to some extent. Graphene has the following advantages in its use as a positive and negative electrode material for lithium ion batteries:
1) Graphene has an extra large specific surface area (2630 m2/g), which can reduce the polarization of the battery and reduce the energy loss caused by polarization.
2) Graphene has excellent electrical and thermal conductivity properties, that is, it has good electron transport channels and stability.
3) The scale of graphene sheets is on the order of micro-nano, much smaller than that of bulk graphite, which makes the diffusion path of Li+ between graphene sheets shorten; the increase of sheet spacing is also beneficial to the diffusion and transport of Li+. Conducive to the improvement of the power performance of lithium-ion batteries.
The following summarizes the application and advantages of graphene in lithium battery positive and negative electrode materials.
1. Application of graphene in anode materials of lithium ion batteries
Graphene directly as a negative electrode material for lithium ion batteries
Advantages of direct storage of graphene: 1) High specific capacity: Lithium ion has non-stoichiometric embedding and deintercalation in graphene, specific capacity up to 700~2000 mAh/g; 2) high charge and discharge rate: The interlayer distance of the layered graphene material is significantly larger than the layer spacing of the graphite, which is more favorable for the rapid embedding and deintercalation of lithium ions. Most studies have also shown that the capacity of the graphene anode is about 540 mA·h/g. However, due to the decomposition of a large amount of oxygen-containing groups on the surface during the charge and discharge process or the reaction with Li+, the capacity of the battery is attenuated, and the rate performance is also affected. Great impact.
The defects caused by the doping of heteroatoms will change the surface morphology of the graphene anode material, thereby improving the wettability between the electrode and the electrolyte, shortening the distance of electron transfer inside the electrode, and improving the diffusion and diffusion of Li+ in the electrode material. Speed, thereby improving the electrical conductivity and thermal stability of the electrode material. For example, the doped N and B atoms can deform the structure of graphene (Fig. 1), charge and discharge at a rate of 50 mA/g, the capacity is 1540 mAh/g, and the graphene material after doping with N and B can be Fast charge and discharge in a short period of time, the battery charge time is 30s at a fast charge and discharge rate of 25A / g.
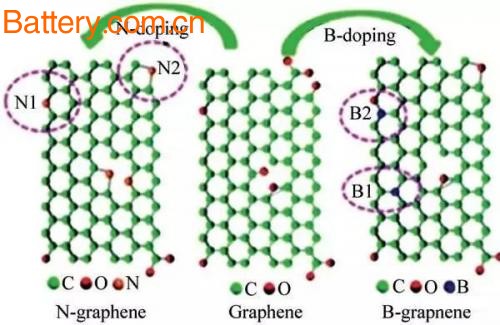
Figure 1 Schematic diagram of the bonding structure of N and B doping in the graphene lattice
However, graphene materials still have some shortcomings as battery anodes, including: 1) The single-layer graphene sheets prepared are extremely easy to accumulate, and the reduction of specific surface area makes them lose some of the high lithium storage space; 2) the first Coulomb efficiency is low, Generally less than 70%. Due to the large specific surface area and abundant functional groups, the electrolyte will decompose on the graphene surface during the cycle to form the SEI film. At the same time, the residual oxygen-containing groups on the surface of the carbon material will irreversibly react with the lithium ions, causing further decline of the reversible capacity. 3) initial capacity attenuation is fast; 4) voltage platform and voltage hysteresis. Therefore, in order to solve this series of problems, the synthesis of graphene and other materials into graphene-based composite anode materials has become a hot spot in the research of lithium batteries and a development direction of lithium battery anode materials.
Graphene and transition metal oxide composite
Transition metal oxide is a lithium battery anode material with broad application prospects. The transition metal oxide has a large specific surface area, a high theoretical lithium storage capacity (greater than 600 mAh/g), a long cycle performance, and a good rate performance. However, the low electrical conductivity of the transition metal oxide and the volume effect caused by Li+ during the intercalation and deintercalation process result in its degradation and instability as a negative electrode material for lithium ion batteries. There are graphene-added transition metal oxides, and the two materials have complementary advantages as a negative electrode material for lithium ion batteries. The advantages can be summarized as follows: 1) Graphene molecules can effectively avoid the agglomeration of transition metal oxides in the charge and discharge cycle; 2) Graphene can improve the conductivity of transition metal oxide materials, and the flexible and crimped sheet structure can be effective. To alleviate the volume expansion during charge and discharge, thereby maintaining the stability of the electrode material; 3) the addition of the transition metal oxide effectively avoids the agglomeration between the graphene sheets and maintains the high specific surface area of ​​the graphene material. The active site on the surface provides additional lithium storage space.
Graphene/Co3O4 composites are typical representatives of such composite anode materials. Reducing the size of Co3O4 or heteroatom doping of graphene can effectively improve the electrochemical performance of such materials. Pyridinium and pyrrole nitrogen in N-doped graphene materials are beneficial to the growth of Co3O4, and are beneficial to the dispersion of metal oxide nanoparticles, thereby reducing the oxygen content of graphene and avoiding the occurrence of irreversible side reactions, thus making the first The charge and discharge coulombic efficiency is improved.
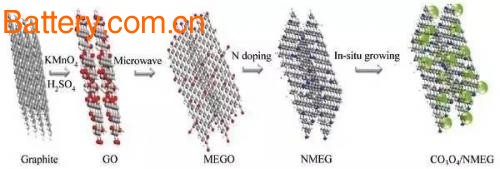
Figure 2 Schematic diagram of Co3O4/NMEG composite preparation
In order to prevent the use of binders and current collectors from affecting the conductivity and capacity properties of the materials, researchers have made MnO2 nanoflakes directly grown on foamed graphene nanotemplates to form electrodes for use as lithium anodes 4. It can be seen from Fig. 3 that the MnO2 skeleton grown on the graphene sheets has a petal shape, and the composite material has a larger specific surface area. The effective contact area between the electrode and the electrolyte is increased, and more active sites are provided during the charging and discharging process, so that the capacity performance, rate performance and cycle performance are greatly improved. After 300 cycles at a current density of 500 mA/g, the capacity is 1200 mAh/g.
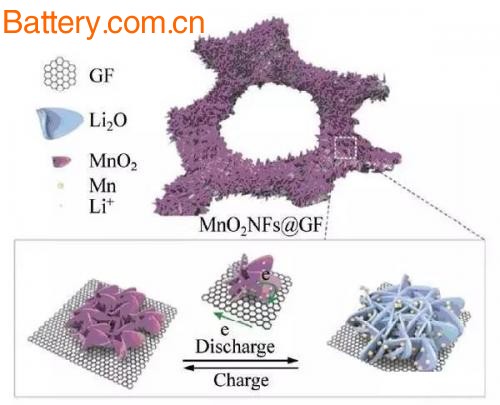
Fig. 3 Schematic diagram of charge and discharge behavior of interconnected MnO2NFs@@GF structure
Graphene is compounded with silicon-based and tin-based materials
Silicon-based and tin-based materials have a high theoretical specific capacity, but when Li+ is embedded and removed, the volume of the electrode material changes significantly. After repeated charge and discharge, the electrode material is easily pulverized and dropped, thereby reducing the battery capacity.
For SnO2, the retaliation of carbon nanomaterials can effectively solve the problem of volume expansion, and prevent the material nanoparticles from agglomerating while improving the conductivity of the material, thereby exerting the potential of high capacity. For example, the graphene-clad sandwich structure SnO2 material has a unique "sandwich" structure which improves the stability of the electrode material and maximizes the specific surface area of ​​the SnO2 molecule, avoids the agglomeration of the SnO2 molecule, and alleviates the volume expansion. The introduction of graphene interlayers enhances the interrelationship between the nanomolecules, thereby avoiding the use of conductive additives and binders. The first discharge capacity of graphene/SnO2 spherical composites was 1247 mAh/g, which was 41.06% higher than that of graphene/SnO2 nanosheets.
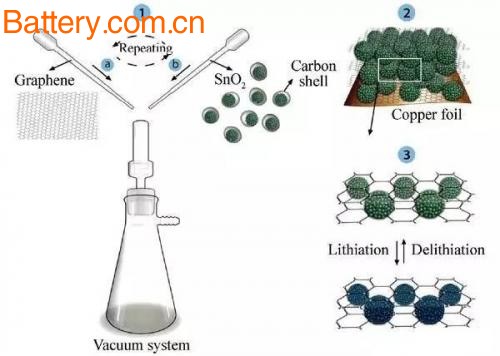
Fig. 4 Schematic diagram of the synthesis process of sandwiched graphene coated SnO2 sphere
The theoretical specific capacity of silicon-based materials is as high as 4200 mAh/g. Its low discharge voltage platform and high natural reserves make it a negative electrode material with excellent application prospects. However, its volume effect is severe during charging and discharging, resulting in poor cycle stability of the material. Similar to tin-based materials, the introduction of graphene can effectively control the volume expansion of silicon-based materials, and the performance of Si anode materials can be improved.
Graphene-coated nano-silicon (GS-Si) composites not only have high capacity, but also have good cycle performance. It can be seen from its scanning electron microscope and transmission electron micrograph that graphene forms a three-dimensional conductive network with internal cavities, which encapsulates the silicon powder well in its internal cavity. The material was tested for constant current charge and discharge at a current density of 200 mA/g. After 30 cycles, the capacity was maintained at 1502 mAh/g and the capacity retention rate was as high as 98%.
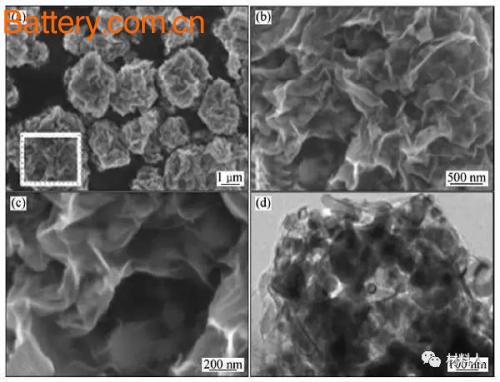
Fig. 5 Scanning electron micrograph and transmission electron micrograph of bath-shaped graphene coated nano-silicon (GS-Si) composite
However, the chemical inertness of the graphene material makes the interaction between it and the Si-based material very weak. After several cycles of charge and discharge, the Si-C structure will be powdered and collapsed. It has been found that the single vacancy defects, double vacancy defects and Stone-Wales defects in graphene due to crystal growth, high energy particle bombardment or chemical treatment can greatly improve the binding energy between graphene/Si molecules, making composite materials Better stability. Deliberate fabrication of such defects increases the adhesion between the graphene material and Si, and vacancy defects can provide additional lithium storage active sites to better increase the capacity of the electrode material. Another way to solve this problem is to grow nano-carbon between Si molecules and graphene sheets. This way, a stable conductive bridge is formed between the graphene nanosheets and the Si-based. This stable conductive network structure is It reduces the volume effect generated during the insertion and removal of Li+, avoids the breakage of the electrode material, and maintains the stability of the SEI film. It avoids excessive capacity attenuation during charge and discharge, and has a very high capacity for Si-based materials. Great help.
2. Graphene composite cathode material
Composite of graphene and polyanionic cathode material
Spinel-type LiMn2O4 and olivine-type LiFePO4 are currently widely used lithium battery cathode materials. However, such materials have poor electron conductivity, too slow Li+ migration, and large resistivity between the electrode and the electrolyte under large rate charge and discharge. In some studies, the introduction of graphene materials has provided a viable solution to these problems. With graphene-modified LiFePO4 and LiMn2O4, the conductivity and rate performance of electrons have been significantly improved. The main reason is that the use of graphene material greatly shortens the diffusion path of lithium ions in the positive electrode material, and the high void ratio inside the composite material also provides a large amount of embedable space for lithium ions, and the lithium storage capacity and energy density are improved. For example, carbon-coated LiFePO4/graphene nanochips (Fig. 6) have a reversible lithium storage capacity of 158 mAh/g and a Coulomb efficiency of over 97% after 100 cycles of charge and discharge at a current density of 17 mA/g. The reversible capacity after charging and discharging at 60 C was 83 mAh/g, and the material had excellent rate performance.
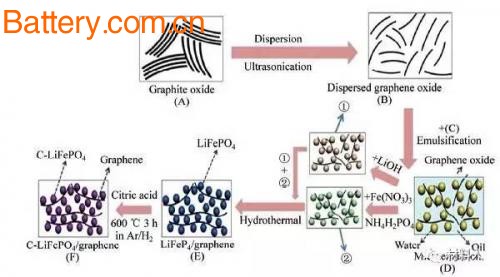
Fig. 6 Schematic diagram of the synthesis mechanism of C-LFP/GNs composites
Graphene and vanadium-based materials
As a positive electrode material for lithium batteries, vanadium-based materials have low cost, high electrochemical activity and high energy density, and have received extensive attention and extensive research by a large number of workers. However, defects such as poor rate performance, high charge transfer resistance, and easy pulverization of the crystal structure of the vanadium-based material restrict its development in practical applications.
Among them, the theoretical specific capacity of VO5 (440 mAh/g) is much higher than that of the current commercial lithium ion battery, and it is a positive electrode material for lithium ion batteries with great potential. The combination of VO5 nanoparticles and graphene to solve the problem of low conductivity and slow lithium ion transmission rate of vanadium-based materials is more. The introduction of graphene material can effectively solve the agglomeration problem between the nanoparticles, so as to more effectively exert the original high capacity potential of VO5. V2O5 is another Vanadium-based material that has attracted much attention. The principle of VO5 is the same, and the introduction of graphene can also improve its rate performance. V2O5 quantum dot/graphene nanocomposite (VQDG), as shown in Figure 7. At the current density of 50, 100, 200, 500 mA / g charge and discharge detection, the capacity retention rate was 100%, 96.92%, 89.16% and 65.72%, respectively.
3. Summary and outlook
For the negative electrode material of lithium battery, the transition metal oxide or the promising Si-based material has been subjected to graphene doping and has been subjected to electrochemical properties such as specific capacity, voltage characteristics, internal resistance, charge and discharge performance, cycle performance, and rate performance. Shows excellent characteristics. The doping of heteroatoms in graphene has introduced more surface defects and improved the electrical conductivity of graphene materials, resulting in better properties of composite materials. The cathode material of lithium battery is similar. The introduction of graphene material into the cathode material system of lithium ion battery can improve the electrical conductivity of the cathode material, protect the cathode material from powdering and collapse, and inhibit the dissolution of the cathode material.
The advantage that graphene exhibits in lithium battery materials is one aspect of the field, and this method is a more feasible method for the electrode material to exert its high capacity potential. After achieving large-scale industrial production of single or several layers of graphene materials, graphene will play an important role in the field of lithium batteries. As far as the current research status is concerned, improving the power and capacity performance of lithium batteries should strengthen the development of new material systems with high capacity characteristics; on the other hand, by constructing reasonable material structures, such as by size and morphology of materials. The regulation of surface defects and other changes in the electrochemical properties of the material, of course, the microstructure of the electrode material itself and how the interaction between the composites affects the electrochemical performance of the material needs further research.
QUANTUM Bucket Elevators have successfully been installed in a wide range of applications and capacities. From process equipment, handling a few kg /hr to over 2000 t/hr with a vast range of materials. Whether your application requires a heavy-duty high capacity machine or an industrial process elevator for your factory.
We have a wealth of experience in designing the correct bucket elevator for your application and have a standard range of elevators, which can be specifically designed for, more specialised applications.
Our elevators have conveyed high temperature, high wear, abrasive, large lumpy, sticky non-flowing materials, as well as free flowing powders and granules. We supply a standard range of twin chain and belt elevators single or twin bucket design for high capacity applications such as grain, minerals and ore. The selection of the elevator depends on the material characteristics and IBS will be able to advise you and select the elevator most suited to your material and your application.
• Gravity elevators
• Positive discharge elevators
• Central discharge slow speed elevators
• Centrifugal elevators
Gravity Type Bucket Elevator
Quantum supply gravity discharge elevators and positive discharge elevators, supplied as close bucket discharge type, central discharge type, or Idler wheel discharge.
Generally a slow speed design gravity bucket elevator is primarily installed for elevating large lumpy & abrasive material. Our standard units are usually chain driven, either friction drive or toothed sprocket.
These elevators offer reliability with minimum wear & a positive discharge emptying of the bucket.
Centrifugal Type Bucket Elevator
Quantum standard range of centrifugal elevators are the most common type of elevator installed to most industries supplied in both belt type or chain type depending on material characteristic and the capacity being elevated and in some case the feeding method of the elevator.
Conveying type
• Segmented tooth sprocket chain type, twin chain or single dropped forged link chain
• Friction chain type elevators, European rolled chain
• Belt elevator. Using rubber belt or 100% polyester solid woven belt, nylon and steel woven belt Typical Construction
• We supply Single leg or Double leg elevators
• Lagged head Pulley
• Slatted return pulley for sticky materials
• Segmented removable sprockets for chain elevators
• Segmented and removable friction pulleys for friction drive elevators
• Fabricated boot and head section assemblies
• Fabricated 3.0m long nominal casings c/w with self-supporting frame and lateral support frames
• Dust tight sealed flanges
• Screw or counterweight tail end take up
Whether the elevator is best suited for toothed sprocket design, friction wheel on conventional belt, IBS will be able to assist with correct selection for the most reliable, maintenance free and cost effective machine to suit your material characteristic and conveying capacity for your particular application.
Types of Buckets readily available
IBS Supply a range of standard off the shelf buckets in a variety of sizes and materials.
Selection of bucket type will depend on material, material characteristics and application. Typical IBS buckets would be plastic-nylon or polyurethane and can be provide FRAS, mild steel fabricated or pressed, stainless steel fabricated or pressed and wear tips for abrasive materials.
Safety and maintenance
• Our equipment is supplied mandatory with anti-roll back device in full load condition
• All inspection doors are fitted with safety limit
• Safety factor of minimum 12: 1 to rated chain pull to installed chain or belt pull under full load stall conditions
For some materials and specific applications, Quantum will design in accordance with Australian standards, suitable explosion venting and will design the structure of the elevator to suit the required application. Typical material that requires this consideration would be sugar, flour, grain and coal.
Standard features for all our bucket elevators
• Qty2 1000mm long inspection doors in conveyor leg and return leg in twin leg elevators for easy inspection of belt or chain and replacement of buckets. Inspection hatch will be provided with bolted mesh screen and safety limit switch
• Qty 2 inspection doors in head section, fitted with safety limit switch• Fully removable split head top section.
• Clean out and inspection doors in Boot section. Self-cleaning boot section optional.
• Under speed sensor and flag disc
• Belt tracking sensor or switch for belt Bucket Elevators
• All our equipment is designed to meet Australian Standards
• Selection of correct conveying velocity and material trajectory for centrifugal elevators is critical to the successful operation of a bucket elevator
• Standard wear plates on boot in-feed and head chute discharge.
• Designed to operate no more than 70% water level of selected bucket at normal operation.
• Installed power capable of full load start up under full bucket surge capacity.
• Our bucket elevators are designed for dust tight design, with suitable dust extraction points
• All our bucket elevators are designed to be self-supporting and are provided with lateral support bracing at approx. 10m centres
Replacement parts service
We can provide a range of standard bucket elevator parts using our standard head and tail pulley assemblies, conveyor belting, elevator butt straps, conveyor bolts and fittings, belt-splicing fittings.
Coupled with our range of standard steel and plastic buckets, elevator chain and fittings, belt tracking switches and sensors we will keep your business moving--
Quantum can provide a customised service contract using experience technicians with many years` experience in servicing and troubleshooting bucket elevators in most states. This service ensures that your equipment is functional to its optimum capabilities and reduces down time parts replacement and potential damage.Our technicians have standard customer maintenance, checking and reporting procedure.
Bucket Elevator,Bucket Conveyor,Elevator Conveyor,Vertical Conveying Elevator
Quantum Conveying Systems Yangzhou Co.,Ltd. , https://www.ycectech.com